|
|
|
GSK980TDi Alarm List and PLC Alarm
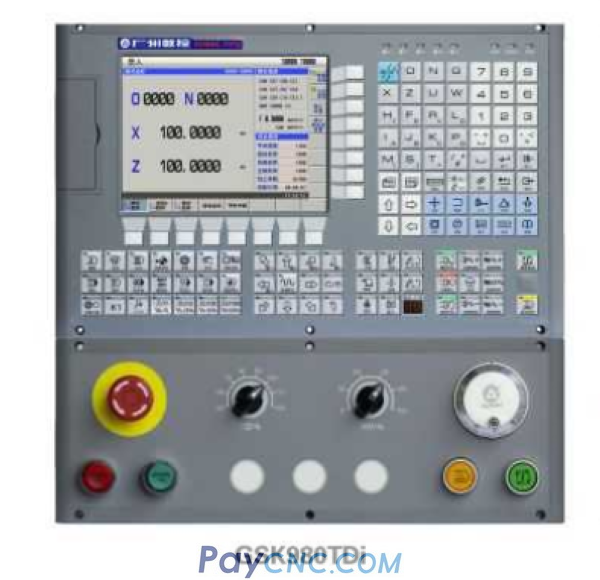
1.CNC alarm
No. |
Content |
Remark |
000 |
Emergent stop alarm and ESP open circuit |
|
001 |
Called programs do not exist or cannot be opened |
|
003 |
Characters are less than 2 or more than 11 for one word |
|
004 |
Address error (address is A~Z) |
|
|
Illegal command value |
|
006 |
Block numbers are negative or with decimals |
|
007 |
Illegal G commands |
|
008 |
Execute G96 when the spindle analog voltage control is invalid |
|
009 |
Command movement distance when G commands in group 00 and 01 are not input and there are invalid commands in group 01 |
|
|
There are the same addresses in one block |
|
011 |
There are more than 40 words in one block |
|
012 |
Command values exceed their valid range or command addresses which cannot be omitted is omitted |
|
013 |
Input S commands except for S00~S99 when the spindle analog voltage control is invalid |
|
014 |
G commands in group 00, 01 and 12 cannot be in the same one block |
|
|
Execute M commands for spindle automatic gear shifting when the spindle analog voltage control is invalid |
|
016 |
Tool offset numbers exceed their valid range(0~32) |
|
017 |
Tool number exceeds the range of No.084 parameter |
|
018 |
The data specified by the interpolation command cannot form a correct curve |
|
019 |
The tool group number exceeds the range( 1~32) in the tool life management |
|
|
Cannot execute T command in C tool nose radius compensation, cancel it |
|
0021 |
G71~G78,G90,G92,G94 can only be used in G18 plane |
|
0022 |
Forbid to use plane exchange code G17~G19 here |
|
0023 |
The programming radius of G05 code is out of allowable range |
|
024 |
There is no G11 or G13.1 in the program |
|
|
There is no tool in the current tool group in the tool life management |
|
026 |
The current tool group has not been defined in the tool life management |
|
027 |
The tool quantity exceeds 8 in the current tool group in tool life management |
|
028 |
The tool life management function is invalid and G10 L3 cannot be used |
|
|
G17~G19 codes Cann't be executed in C tool compensation or cylindrical interpolation |
|
032 |
Absolute value of R is more than that of U/2 in G90, G92,G92.1 |
|
033 |
Absolute value of R is more than that of W in G94 |
|
040 |
There are more than 100 blocks in G70~G73 |
|
041 |
Ns and Nf are reversed each other in G70~G73 |
|
042 |
There is no Ns or Nf or they exceed their allowed range in G70~G73 |
|
No. |
Content |
Remark |
043 |
There is no Ns or Nf in G70~G73 |
|
044 |
Call subprograms in G70~G73 |
|
045 |
Ns does not command G00 or G01 in G70~G73 |
|
046 |
Initial blocks are employed with the forbidden G commands in G70~G73 |
|
047 |
Unusable G code is in the block specified by Q in G70,G71,G72,G73 |
|
050 |
G71~G72 command can't satisfy the condition of single increase or decrease |
|
051 |
Single infeed exceeds its allowed range in G71 or G72 |
|
052 |
Single tool retraction exceeds its allowed range in G71 or G72 |
|
053 |
The cycle starting point is in the closed area formed by the starting point and end point of the finishing path in G71 or G72 |
|
054 |
Flute quantity is more than 10 in G71 or G72 |
|
055 |
X/ Z value is not specified in the first block or the movement is 0 in G71 |
|
056 |
X/ Z value is not specified in the first block or the movement is 0 in G72 |
|
057 |
Cycle times is less than 1 or more than 99999 in G73 |
|
060 |
Single tool retraction R(e) exceeds its allowed range in G74 or G75 |
|
061 |
The tool retraction is negative at the end of cutting in G74 or G75 |
|
0062 |
Z value is 0 or not input in G74 |
|
0063 |
Q is in default or out of range in G74 |
|
0064 |
X single cutting value(P) exceeds its allowed range in G74 |
|
0065 |
X value is 0 or not input in G75 |
|
0066 |
P is in default or out of range in G75 |
|
0067 |
Z single cutting value(Q) exceeds its allowed range in G75 |
|
0069 |
Starting point coordinates are abnormal when cycle ends and returns to starting point |
|
0070 |
The tool starts from the midway in taper screw thread cutting in G76/G78 |
|
0071 |
Min. cutting value exceeds its allowed range in G76 or G78 |
|
0072 |
Finishing allowance exceeds its allowed range in G76 or G78 |
|
0073 |
Tooth height is less than finishing allowance or 0 in G76 or G78 |
|
0074 |
Cycle times exceeds its allowed range in G76 or G78 |
|
0075 |
X/Z movement distance in G76 is zero |
|
0076 |
There is no specified tooth height P in G76 or G78 |
|
0077 |
There is no the first cutting depth Q or Q is 0 or Q is not input in G76 or G78 |
|
0078 |
Tool nose angle is more than or equal to thread angle in G76 or G78 |
|
0079 |
Cutting value of G78 is out of range(0,1) |
|
0080 |
Cutting mode of G78 is out of range(0,1,2,3) |
|
0082 |
Have no the measured position arrival signal in parameter specifying area in automatic tool offset(G36,G37) |
|
0083 |
Specifying an invalid axis or a command is incremental in automatic tool offset (G36,G37). Modify the program |
|
0084 |
Have the measured position arrival signal in area set by the parameter in automatic tool offset(G36,G37) |
|
0085 |
The distance between the starting point and the target is less than the setting (142,143) in automatic tool offset(G36,G37), have no set the rapid motion area |
|
No. |
Content |
Remark |
0086 |
The parameter (142,144) or (143,145) area setting are wrong in automatic tool offset(G36,G37) |
|
0087 |
Firstly create or set the coordinate system before executing G36,G37 |
|
0088 |
Firstly set the correct tool number and the compensation number before executingG36,G37 |
|
0089 |
The tool offset is in protection state, and cannot be written |
|
0090 |
When tool offset measure executes the direction input B operation, axis movement directions are interlocked |
|
0092 |
Can't find the thread repair position. An soft key [THD.REPAIR RECORD POS] displayed on the ABSOLUTE screen. In JOG,HND or STEP mode, press the key record the thread repair position. |
|
0093 |
The thread repair position beyond the thread repair program, please check the program and the thread repair position |
|
0095 |
Subprogram numbers are not input or are illegal when M98 calls them |
|
0096 |
Layers of nested subprograms are more than 4 |
|
0097 |
Calling programs in M98 is the current one(main program) |
|
0099 |
Use M98 or M99 in C tool radius compensation |
|
0103 |
Denominator is 0 for division operation in G65 |
|
0104 |
G65 commands illegal H command |
|
0105 |
Macro variable number of G65 is illegal(error) |
|
0109 |
P command value isn’t variable in G65 |
|
0111 |
H99 user alarm number in G65 exceeds its range |
|
0112 |
Block number of macro command (G65)skip or M99 program return exceeds their range |
|
0113 |
There is no block number for block skip or M99 program return |
|
0114 |
G65, G66 command format are mistaken |
|
0115 |
G65 H operand is mistaken |
|
0116 |
G code format of calling macro program is err |
|
0118 |
Number of argument I, J, K cannot exceed 10 |
|
0120 |
P value of G30 code is out of range (2~4) |
|
0122 |
G22,G23 command code can not be executed with other G,M,S,T command simultaneously |
|
0123 |
Stored travel check function has been closed,Can't use G22,G23 command code. modify parameter No.172 please. |
|
0129 |
Programmed axis name is invalid |
|
0130 |
axis address is not normative |
|
0131 |
G31/G32/G32.1/G33/G34/G36/G37/G84/G88/auxiliary axis code can't be used in C offset type |
|
0133 |
Specified axis is a linearity of cylinder or rotary axis |
|
0134 |
Cannot specify the cylinder radius again |
|
0135 |
The linear or rotary axis setting used to the cylinder interpolation is mistaken |
|
0136 |
Only currently use the tool nose direction T0 or T9 to create C tool compensation |
|
0140 |
The macro format is specified in error |
|
0141 |
DO,END tabs are not 1,2,3 in macro statement |
|
0142 |
DO,END formats are specified in error |
|
No. |
Content |
Remark |
0143 |
The brackets are not matched in macro statement or the format is specified in error |
|
0144 |
The divisor in macro statement cannot be 0 |
|
0145 |
The specified anti-tangent ATAN format is mistaken in macro statement |
|
0146 |
The anti logarithm of LN in macro statement is 0 or less than 0 |
|
0147 |
The square root in macro statement cannot be negative |
|
0148 |
The tangent TAN result in macro statement is endless |
|
0149 |
The operands of anti sine or anti cosine in macro statement exceed the range between -1 and 1 |
|
0150 |
The macro variable number or the variable value is illegal(error) in macro statement |
|
0151 |
The local variable is empty |
|
0152 |
The variable #0 is always empty and cannot be operated |
|
0153 |
The operand in macro statement is not binary |
|
0154 |
P value don't want to be defined while calling macro program of using G code |
|
0155 |
Format of program note is mistaken (mismatching) |
|
0156 |
G20,G21 command code can not be executed with other command simultaneously |
|
0157 |
Metric/Inch system has been changed,and will be effective after restart |
|
0174 |
Some parameters cann't be modified for current operation level |
|
0175 |
W value or macro variety value of W is out of range while writing parameters |
|
0176 |
W value or macro variety value of W is not a valid binary value while writing parameters |
|
0177 |
Not specify writing or reading operand under the state of writing or reading parameters |
|
0178 |
Not specify a parameter or the parameter don't exist under the state of writing or reading parameters |
|
0179 |
Not specify axis NO. when writing or reading axis parameters |
|
0180 |
R only specify macro variety under the state of writing or reading parameters |
|
0181 |
The axis NO. of setting is out of range while writing or reading parameters |
|
0182 |
Specify simultaneously a operand of writing and reading in one program segment under the state of writing or reading parameters |
|
0183 |
Operand cann't be a decimal fraction under the state of writing or reading parameter |
|
0184 |
Specify two or above parameters in one program segment under the state of writing or reading parameters |
|
0185 |
Parameter NO. cann't be a decimal fraction under the state of writing or reading parameters |
|
0190 |
Not specify screw pitch or out of range in machinning screw or tap |
|
0191 |
Head quantity of multi-thread is out of range |
|
0192 |
Initial angle of screw (Q value) is out of range |
|
0193 |
Nonzero move value of X axis has been commanded in G33 |
|
0194 |
Y axis can't interpolate with X/Z axis in G33 |
|
0195 |
R value of G34 is out of range |
|
No. |
Content |
Remark |
0200 |
Circle radius is zero or undefined |
|
0201 |
The distance of circle start and end point is too small |
|
0202 |
Circle start point and center of the circle are the same as one point |
|
0203 |
The error of circle radius is out of range of the parameter NO.154 |
|
0204 |
Not specify middle point in three point circle instruction |
|
0205 |
Three points are a line in three point circle instruction |
|
0206 |
Helical interpolation is invalid if defined plane hasn't movement |
|
0208 |
Long radius or short radius of ellipse is zero or undefined |
|
0209 |
P value of parabola is zero or undefined |
|
0227 |
Spindle positioning axis isn't allowed to execute the function |
|
0228 |
Spindle positioning axis and some code cann't be in the same block |
|
0229 |
Unusable code or command in synchro control |
|
0232 |
Specify the axis movement command in M29 or G84/G88 |
|
0233 |
Rigid tapping signal (G61.0) in rigid tapping mode is abnormal |
|
0234 |
Specify M29 repetitively or not input M29 before rigid tapping |
|
0235 |
The spindle must be oriented, M29 cannot be with G84/G88 in the same block when rigid tapping |
|
0236 |
Set the axis used to the spindle control to the rotary axis before the rigid tapping/rigid thread machining |
|
0237 |
Have used unnecessary commands in rigid tapping or rigid screw |
|
0238 |
Have not selected the spindle used to the rigid tapping for the multi-spindle function device when rigid tapping |
|
0239 |
Cannot switch the spindle used to the tapping when rigid tapping |
|
0251 |
Mistake in programming causes an error of C tool nose radius compensation |
|
0252 |
Mistake in programming causes an end point of arc machining is not on the arc in the course of C tool nose radius compensation |
|
0253 |
Mistake in programming causes there are the same coordinates for two neighboring points not to execute C tool nose radius compensation |
|
0254 |
Mistake in programming causes there are the same coordinates between center point and starting point of arc not to execute C tool nose radius compensation |
|
0255 |
Mistake in programming causes there are the same coordinates between center point and end point of arc not to execute C tool nose radius compensation |
|
0256 |
Arc radius is less than that of tool nose to cause not to execute C tool nose radius compensation |
|
0257 |
Mistake in programming causes there is not intersection of two arcs of current tool radius in the course of C tool nose radius compensation |
|
0258 |
Specify one arc command as executing C tool nose radius compensation |
|
0259 |
Specify one arc command as canceling C tool nose radius compensation |
|
0260 |
There is excessive cutting as checking C tool nose radius compensation |
|
0261 |
Mistake in programming causes there is not intersection between straight line and arc of current tool radius in the course of C tool nose radius compensation |
|
No. |
Content |
Remark |
0262 |
Mistake in programming causes there is not intersection between arc and straight line of current tool radius in the course of C tool nose radius compensation |
|
0263 |
There are too non movement commands in C too radius compensation, the buffer overflows |
|
0270 |
The circle centre angle of circular screw interpolation is not in the range of 45°~135°or 135°~225°or 225°~315°or -45°~45.modify the program please |
|
0276 |
The end point and angle value using direct input of drawing dimensions are not applicable or normal |
|
0277 |
The instruction isn't allowed in direct input of drawing dimensions or non-motion blocks are too much |
|
0278 |
The middle block using direct input of drawing dimensions cann't be the last block of a loop |
|
0279 |
Angle is not normal or the end point cann't be calculated in direct input of drawing dimensions |
|
0281 |
The linear chamfer length is too length |
|
0282 |
The arc chamfer radius is too big |
|
0283 |
The linear chamfer length is too big or the arc data is mistaken |
|
0284 |
The arc chamfer radius is too big or the arc data is mistaken |
|
0285 |
The linear chamfer length is too big or the arc data is mistaken |
|
0286 |
The arc chamfer radius is too big or the arc data is mistaken |
|
0287 |
The linear chamfer length is too big or the intersection is not on the arc |
|
0288 |
The arc chamfer radius is too big or the intersection is not on the arc |
|
0289 |
The chamfer cannot be executed in end position |
|
0290 |
Cannot start the polar coordinate and the cylinder interpolation in C tool compensation state or G99 |
|
0291 |
The linear axis or rotary axis of the polar coordinates does not correspond to No.189 or the linear axis attribution setting is mistaken |
|
0292 |
Execute the length compensation of all axes before starting the polar coordinates |
|
0293 |
X cannot be negative or 0 in G16/G15 |
|
0294 |
Have used the command which cannot be used to the polar coordinates and the cylinder interpolation |
|
0295 |
C tool compensation is not cancelled in the polar coordinates and the cylinder interpolation |
|
0296 |
Finish machining counts of cylindrical interpolation loop are over 9999 |
|
0297 |
Cann't cut the workpiece in cylindrical interpolation loop because X orientation and cutting direction are not same |
|
6000 |
CNC emergent stop is failure(restart the CNC) |
|
6001 |
No program zero is defined |
|
6003 |
Feed speed is too high |
|
6004 |
Spindle stopped accidentally, please stop feeding and check the spindle |
|
6005 |
Not define the highest speed of some gear, please check the parameter No.37~No.40 |
|
6010 |
Spindle doesn't rotate,or speed is too slow in thread cutting |
|
No. |
Content |
Remark |
6011 |
feed speed exceeds limit speed in cutting(Parameter No.027) |
|
6012 |
Spindle speed fluctuation has exceeded the alarm valve in thread cutting |
|
6013 |
The screw pitch occurs 0 |
|
6014 |
Spindle encoder pulse is out of 100~10000 |
|
6020 |
reference point hadn't found,Don't go back 2nd or 3rd or 4th reference point |
|
6050 |
PLCAxis is working,Don't change Ctrlmode |
|
6051 |
CNCAxis is working,Don't change Ctrlmode |
|
6052 |
PLCAxis is working,CNC can't Ctrl this axis |
|
6053 |
The movement distance of PLC axis is out of range |
|
6054 |
In Ref mode A, the move is fail |
|
6300 |
Stored stroke limit 1 has been exceeded |
|
6301 |
Stored stroke limit 2 has been exceeded |
|
6302 |
Stored stroke limit 3 has been exceeded |
|
6304 |
Reference point is in the limit area of stored stroke limit 1, Please modify parameter No.045, No.046 |
|
6305 |
Reference point is in the limit area of stored stroke limit 2.Please modify parameter No.100, No.101 |
|
6306 |
Reference point is in the limit area of stored stroke limit 3.Please modify parameter No.102, No.103 |
|
6311 |
overtravel in setting positive location of axis X |
|
6312 |
overtravel in setting positive location of axis Z |
|
6313 |
overtravel in setting positive location of axis Y |
|
6314 |
overtravel in setting positive location of axis 4th |
|
6315 |
overtravel in setting positive location of axis 5th |
|
6316 |
overtravel in setting positive location of axis 6th |
|
6321 |
overtravel in setting negative location of axis X |
|
6322 |
overtravel in setting negative location of axis Z |
|
6323 |
overtravel in setting negative location of axis Y |
|
6324 |
overtravel in setting negative location of axis 4th |
|
6325 |
overtravel in setting negative location of axis 5th |
|
6326 |
overtravel in setting negative location of axis 6th |
|
6331 |
The X axis positive location of stored stroke limit 2 has been exceeded |
|
6332 |
The Z axis positive location of stored stroke limit 2 has been exceeded |
|
6333 |
The Y axis positive location of stored stroke limit 2 has been exceeded |
|
6334 |
The 4th axis positive location of stored stroke limit 2 has been exceeded |
|
6335 |
The 5th axis positive location of stored stroke limit 2 has been exceeded |
|
6336 |
The 6th axis positive location of stored stroke limit 2 has been exceeded |
|
6341 |
The X axis negative location of stored stroke limit 2 has been exceeded |
|
6342 |
The Z axis negative location of stored stroke limit 2 has been exceeded |
|
6343 |
The Yaxis negative location of stored stroke limit 2 has been exceeded |
|
6344 |
The 4th axis negative location of stored stroke limit 2 has been exceeded |
|
6345 |
The 5th axis negative location of stored stroke limit 2 has been exceeded |
|
6346 |
The 6th axis negative location of stored stroke limit 2 has been exceeded |
|
6351 |
The X axis positive location of stored stroke limit 3 has been exceeded |
|
6352 |
The Z axis positive location of stored stroke limit 3 has been exceeded |
|
No. |
Content |
Remark |
6353 |
The Y axis positive location of stored stroke limit 3 has been exceeded |
|
6354 |
The 4th axis positive location of stored stroke limit 3 has been exceeded |
|
6355 |
The 5th axis positive location of stored stroke limit 3 has been exceeded |
|
6356 |
The 6th axis positive location of stored stroke limit 3 has been exceeded |
|
6361 |
The X axis negative location of stored stroke limit 3 has been exceeded |
|
6362 |
The Z axis negative location of stored stroke limit 3 has been exceeded |
|
6363 |
The Y axis negative location of stored stroke limit 3 has been exceeded |
|
6364 |
The 4th axis negative location of stored stroke limit 3 has been exceeded |
|
6365 |
The 5th axis negative location of stored stroke limit 3 has been exceeded |
|
6366 |
The 6th axis negative location of stored stroke limit 3 has been exceeded |
|
6411 |
axis X+ overtravel |
|
6412 |
axis Z+ overtravel |
|
6413 |
axis Y+ overtravel |
|
6414 |
axis 4th+ overtravel |
|
6415 |
axis 5th+ overtravel |
|
6416 |
axis 6th+ overtravel |
|
6421 |
axis X- overtravel |
|
6422 |
axis Z- overtravel |
|
6423 |
axis Y-overtravel |
|
6424 |
axis 4th- overtravel |
|
6425 |
axis 5th- overtravel |
|
6426 |
axis 6th- overtravel |
|
6431 |
The axis X driver is not prepared |
|
6432 |
The axis Z driver is not prepared |
|
6433 |
The axis Y driver is not prepared |
|
6434 |
The axis 4th driver is not prepared |
|
6435 |
The axis 5th driver is not prepared |
|
6436 |
The axis 6th driver is not prepared |
|
6441 |
Spindle servo 1 is not ready |
|
6442 |
Spindle servo 2 is not ready |
|
6443 |
Spindle servo 3 is not ready |
|
6500 |
Slave device number conflict in GSKLINK communication |
|
6600 |
The bus connection is OFF |
|
6601 |
Enumberation overtime |
|
6602 |
The bus connection creating communication fails |
|
6603 |
The bus connection delaying causes the test device to fail |
|
6604 |
The bus communication's parameterr allocation fails |
|
6605 |
The bus communication allocation overtime |
|
6606 |
The bus main station's communication returns to CP0 stage |
|
6607 |
The slave station number set by the system is inconsistent with the actual |
|
6608 |
The slave device's axis name (logic address) is not matched with the system's valid axis |
|
6610 |
MDT data loss |
|
6611 |
MST data loss |
|
6612 |
MDT data check error |
|
No. |
Content |
Remark |
6613 |
GDT data check error |
|
6620 |
IDN16, 24 allocation fails |
|
6621 |
IDN32,35 allocation fails |
|
6622 |
IDN5030,5031,5033 allocation fails |
|
6630 |
I/O unit allocation fails |
|
6702 |
Setup machine zero point again please. Because the parameter file of zero point failed to save as using absolute encoder motor |
|
6703 |
Setup machine zero point again please. Because the parameter file of zero point failed to read as using absolute encoder motor. |
|
6711 |
The error of actual position and memory position oversteps the range permitted as axis X equipped absolute encoder. Return machine zero point manually and set zero point again. |
|
6712 |
The error of actual position and memory position oversteps the range permitted as axis Z equipped absolute encoder. Return machine zero point manually and set zero point again |
|
6713 |
The error of actual position and memory position oversteps the range permitted as axis Y equipped absolute encoder. Return machine zero point manually and set zero point again |
|
6714 |
The error of actual position and memory position oversteps the range permitted as axis 4TH equipped absolute encoder. Return machine zero point manually and set zero point again. |
|
6715 |
The error of actual position and memory position oversteps the range permitted as axis 5TH equipped absolute encoder. Return machine zero point manually and set zero point again. |
|
6716 |
The error of actual position and memory position oversteps the range permitted as axis 6TH equipped absolute encoder. Return machine zero point manually and set zero point again. |
|
6721 |
Initialization of machine coordinates makes a mistake while starting as axis X equipped absolute encoder. Reset machine zero point again. |
|
6722 |
Initialization of machine coordinates makes a mistake while starting as axis Z equipped absolute encoder. Reset machine zero point again. |
|
6723 |
Initialization of machine coordinates makes a mistake while starting as axis Y equipped absolute encoder. Reset machine zero point again. |
|
6724 |
Initialization of machine coordinates makes a mistake while starting as axis 4TH equipped absolute encoder. Reset machine zero point again |
|
6725 |
Initialization of machine coordinates makes a mistake while starting as axis 5TH equipped absolute encoder. Reset machine zero point again. |
|
6726 |
Initialization of machine coordinates makes a mistake while starting as axis 6TH equipped absolute encoder. Reset machine zero point again. |
|
6741 |
When X axis is allocated with an absolute encoder without a reference point, a reference point is set after the machine is debugged normally |
|
6742 |
When Z axis is allocated with an absolute encoder without a reference point, a reference point is set after the machine is debugged normally |
|
6743 |
When Y axis is allocated with an absolute encoder without a reference point, a reference point is set after the machine is debugged normally |
|
No. |
Content |
Remark |
6744 |
When 4th axis is allocated with an absolute encoder without a reference point, a reference point is set after the machine is debugged normally |
|
6745 |
When 5th axis is allocated with an absolute encoder without a reference point, a reference point is set after the machine is debugged normally |
|
6746 |
When 6th axis is allocated with an absolute encoder without a reference point, a reference point is set after the machine is debugged normally |
|
6751 |
Gear ratio of CNC or servo ,the direction of axis moving and the machine zero points are not as different as data established successfully while axis X equipped absolute encoder. Check up parameters and renew to set machine zero points |
|
6752 |
Gear ratio of CNC or servo ,the direction of axis moving and the machine zero points are not as different as data established successfully while axis Z equipped absolute encoder. Check up parameters and renew to set machine zero points. |
|
6753 |
Gear ratio of CNC or servo ,the direction of axis moving and the machine zero points are not as different as data established successfully while axis Y equipped absolute encoder. Check up parameters and renew to set machine zero points. |
|
6754 |
Gear ratio of CNC or servo ,the direction of axis moving and the machine zero points are not as different as data established successfully while axis 4TH equipped absolute encoder. Check up parameters and renew to set machine zero points. |
|
6755 |
Gear ratio of CNC or servo ,the direction of axis moving and the machine zero points are not as different as data established successfully while axis 5TH equipped absolute encoder. Check up parameters and renew to set machine zero points. |
|
6756 |
Gear ratio of CNC or servo ,the direction of axis moving and the machine zero points are not as different as data established successfully while axis 6TH equipped absolute encoder. Check up parameters and renew to set machine zero points. |
|
6761 |
The batteries of absolute encoder are too low as axis X equipped absolute encoder. Renew batteries and set machine zero point again. |
|
6762 |
The batteries of absolute encoder are too low as axis Z equipped absolute encoder. Renew batteries and set machine zero point again. |
|
6763 |
The batteries of absolute encoder are too low as axis Y equipped absolute encoder. Renew batteries and set machine zero point again. |
|
6764 |
The batteries of absolute encoder are too low as axis 4th equipped absolute encoder. Renew batteries and set machine zero point again. |
|
6765 |
The batteries of absolute encoder are too low as axis 5th equipped absolute encoder. Renew batteries and set machine zero point again. |
|
6766 |
The batteries of absolute encoder are too low as axis 6th equipped absolute encoder. Renew batteries and set machine zero point again. |
|
6771 |
Machine zero point Can't be returned because no zero point position is established as axis X of equipping absolute encoder |
|
6772 |
Machine zero point Can't be returned because no zero point position is established as axis Z of equipping absolute encoder |
|
No. |
Content |
Remark |
6773 |
Machine zero point Can't be returned because no zero point position is established as axis Y of equipping absolute encoder |
|
6774 |
Machine zero point Can't be returned because no zero point position is established as axis 4TH of equipping absolute encoder |
|
6775 |
Machine zero point Can't be returned because no zero point position is established as axis 5TH of equipping absolute encoder |
|
6776 |
Machine zero point Can't be returned because no zero point position is established as axis 6TH of equipping absolute encoder |
|
6781 |
The position of movining is being out of range as axis X of equipping absolute encoder |
|
6782 |
The position of movining is being out of range as axis Z of equipping absolute encoder |
|
6783 |
The position of movining is being out of range as axis Y of equipping absolute encoder |
|
6784 |
The position of movining is being out of range as axis 4TH of equipping absolute encoder |
|
6785 |
The position of movining is being out of range as axis 5TH of equipping absolute encoder |
|
6786 |
The position of movining is being out of range as axis 6TH of equipping absolute encoder |
|
|
|
|
7001 |
The name of axis isn't in the usable range or exists same name with others,set parameter #225 |
|
7002 |
increment system of additional axis(Y,4th,5th) should not less than current increment system(IS-B,IS-C).setting again |
|
7003 |
basic axis X/Y/Z can only set one,set parameter #230 |
|
7008 |
parameters of electric-gear set wrong |
|
7009 |
data errors!restart and return reference please! adjust tool offsets,check all parameters. |
|
7010 |
can't set two or more CS axes effectively if muilt-spindles function are not effect or if no using second CS axis |
|
7011 |
Can't use CS spindle because the spindle don't bind a valid feed axis. Please check the parameter No.221 |
|
7012 |
Set rotary axis function firstly before using CS axis or rigid tapping. |
|
7013 |
Can't use axis CS because it isn't a serial spindle. |
|
7014 |
Fail to switch CS mode |
|
7015 |
don't switch spindle working mode while using Cs axis |
|
7016 |
Set rotary axis function firstly before using CS axis or rigid tapping |
|
7017 |
Can't use axis CS because it isn't a serial spindle. |
|
7020 |
Spindle No. definition error or repeated please set parameter No.220 |
|
7021 |
The feed axis which binds to spindle is set by error or repeated. Please check the parameter No.221 |
|
7022 |
The feed axis which binds to spindle is invalid or CS axis at first. Then the function of servo motor spindle can be used. |
|
No. |
Content |
Remark |
7023 |
There isn't a feed axis which binds to spindle. Can’t use spindle function of servo motor. Please check parameter No.221 |
|
7024 |
Spindle positioning axis can't move in manual |
|
7030 |
Synchronous control master axis and slave axis cannot return to reference |
|
7031 |
Synchronous axis no.incorrect,duplicated or axis is invalid. Modify parameter No.197~No.199 please. |
|
7035 |
Function is invalid due to detecting signal add settting incorrect. modify parameter No.136~No.139 please |
|
7037 |
The coordinates switched is out of range when G54~G59 coordinates system switchs.Return machine zero point and set tool offset again please. |
|
7100 |
Nvram data error(CurMachCoord,CurAbsCoord,CurRelCoord) Restart machine and set zero point and set tool offset again please. |
|
7101 |
Nvram data error(MlkAbsCoord,MlkRelCoord,PoffMlkState) Restart machine and return zero point and set tool offset again please. |
|
7102 |
Nvram data error(LocalCoordOFT) Restart machine and return zero point and set tool offset again please. |
|
7103 |
Nvram data error(MoveDirIsPlus) Restart machine and return zero point and set tool offset again please. |
|
7104 |
Nvram data error(OffsUnmoved) Restart machine and return zero point and set tool offset again please. |
|
7105 |
Nvram data error(Last_Toffs) Restart machine and return zero point and set tool offset again please. |
|
7106 |
Nvram data error(ToffsUnmoved) Restart machine and return zero point and set tool offset again please. |
|
7107 |
Nvram data error(OffsRcd) Restart machine and return zero point and set tool offset again please. |
|
7108 |
Nvram data error(OffsRcdts) Restart machine and return zero point and set tool offset again please. |
|
7109 |
Nvram data error(LOffsDiff) Restart machine and return zero point and set tool offset again please. |
|
7110 |
Nvram data error(CompPos) Restart machine and return zero point and set tool offset again please. |
|
7111 |
Nvram data error(CurCoordSys) Restart machine and return zero point and set tool offset again please. |
|
7112 |
Nvram data error(CNC_CurrentToolNo, CNC_CurrentTComp, CurrentRoffsmode) Restart machine and return zero point and set tool offset again please. |
|
7113 |
Nvram data error(ToffLock) Restart machine and return zero point and set tool offset again please. |
|
7114 |
Nvram data error(PubMacroBuf_S) Restart machine and return zero point and set tool offset again please. |
|
7115 |
Nvram data error(APCRefPos) Restart machine and set zero point and set tool offset again please. |
|
7116 |
Nvram data error(RefCurMachCoord) Restart machine and set zero point and set tool offset again please. |
|
No. |
Content |
Remark |
7117 |
Nvram data error(BLashSum) Restart machine and set zero point and set tool offset again please. |
|
7118 |
Nvram data error(PitchSum) Restart machine and set zero point and set tool offset again please. |
|
7120 |
Nvram data error(TSafetyPos) Restart machine and set safe position of switching tool please. |
|
7801 |
Parameter switch has been opened |
|
7803 |
Fail to open or delete the part program |
|
7804 |
Set position number of screw compensation error. modify parameter No.96 ~ 98 please.。 |
|
7805 |
USB disk connectted again. please reload the program if the file has been modified! |
|
7806 |
turn on power again when parameter is modified |
|
7807 |
Success to renew the working ladder which has been stopped.rerun it or power on again please. |
|
7808 |
CNC is failed to communicate with keyboard |
|
7810 |
Fail to open PLC file |
|
7811 |
The software version of ladder_chart is not suited |
|
7812 |
The first grade program of ladder_chart is too long |
|
7815 |
The voltage is low or unsteady. |
|
7816 |
NVRAM data verifies error! |
|
7817 |
The time is too short to save NVRAM data for last time when lost power. |
|
7830 |
Machine diagnosis configuration file is modified, it is better to restart again. |
|
7900 |
Loaded system allocation file is mistaken. Confirm whether cnc.cfg. exists |
|
7901 |
Loaded system allocation file is mistaken. Confirm whether param.cfg. exists |
|
7902 |
Loaded parameter value file is mistaken |
|
7903 |
Tool offset error!Refresh tool offset please. Clear alarm for pressing keys [CAN],[RESET] simultaneously |
|
7904 |
Loaded pitch compensation file is mistaken |
|
7905 |
Fail to load file COORD.CRD |
|
7906 |
Fail to start PLC ladder Check ladder! |
|
7908 |
Fail to load toollife file! |
|
7909 |
Limited-time stop time is over and the system cannot run normally. Please contact with salesmen |
|
7910 |
CNC level degrade to lowest beause the time of stopping has been arrived,contact your supplier please. |
|
7911 |
CNC is going to stop work in several days. Contact with supplier in advance please. |
|
7912 |
The password of stopping operation is default.Suggest to change the password please. |
|
7998 |
System software error! please contact with GSK CNC equipment co.,ltd.! |
|
7999 |
There is an unknown alarm. Please contact with developers。 |
|
2.PLC alarm (standard PLC ladder definition )
Address |
Alarm No. |
Content |
A0000.0 |
1000 |
Tool change time is too long |
A0000.1 |
1001 |
Alarm for the tool is not in-position when tool change ends |
A0000.2 |
1002 |
Alarm for the tool change is not completed |
A0000.3 |
1003 |
Alarm for the system has not received the lock signal |
A0000.4 |
1004 |
The system repetitively checks the lock signal and the lock signal is invalid when tool change is done |
A0000.5 |
1005 |
Tool change makes mistakes before the system is turned off |
A0000.6 |
1006 |
Pre-indexing proximity switch does not reach |
A0000.7 |
1007 |
Alarm for tool post overheat |
A0001.0 |
1008 |
Tailstock function is invalid, and M10 and M11 cannot be executed |
A0001.1 |
1009 |
The thread run-out cannot be executed when the spindle rotating |
A0001.3 |
1011 |
Have not checked the tailstock forward and cannot start the spindle |
A0001.4 |
1012 |
Tool change mode A and B can have up to 8 tools |
A0001.5 |
1013 |
Tool use life ends |
A0001.6 |
1014 |
Confirm tool number of tool post (8, 10, 12) |
A0001.7 |
1015 |
Confirm tool number of tool post (6, 8, 10, 12) |
A0002.0 |
1016 |
Alarm for protection door not closed |
A0002.1 |
1017 |
Alarm for pressure low |
A0002.3 |
1019 |
Can’t release chuck when spindle rotating |
A0002.4 |
1020 |
Alarm for disabled clamping in-position signal when spindle rotating |
A0002.5 |
1021 |
Can’t start spindle when disabled clamping in-position signal |
A0002.6 |
1022 |
Can’t start spindle when chuck is released |
A0003.0 |
1024 |
Can’t execute M12 or M13 with disabled chuck function |
A0003.1 |
1025 |
Have not checked chuck clamping/releasing in-position signal |
A0003.3 |
1027 |
Tool pot is not released or lock signal is not cancelled |
A0003.4 |
1028 |
Has not found the target tool number |
A0003.5 |
1029 |
Has not received tool pot stop and locking start signal |
A0004.0 |
1032 |
Illegal M code |
A0004.1 |
1033 |
The current spindle is not analog, and Jog function cannot be executed |
A0004.2 |
1034 |
M03,M04 specification are mistaken |
A0004.3 |
1035 |
M63,M64 specification are mistaken |
A0004.4 |
1036 |
Spindle gear shift time is too long |
A0004.5 |
1037 |
Spindle speed/position control switch time is too long |
A0004.6 |
1038 |
The 2nd spindle speed/position control switch time is too long |
A0004.7 |
1039 |
Spindle position control does not permit orientation |
A0005.0 |
1040 |
Spindle orientation time is too long |
A0005.1 |
1041 |
Alarm for the abnormal spindle servo or frequency converter for abnormality |
A0005.2 |
1042 |
Alarm for the abnormal 2nd spindle servo or frequency converter |
A0005.3 |
1043 |
Forbid clamping the spindle when the spindle rotating or feeding |
A0005.4 |
1044 |
Spindle is clamped not to rotate or feed |
A0007.0 |
2000 |
Hydraulic motor is not started |
A0007.1 |
2001 |
Safety door has been opened |
A0007.3 |
2003 |
Alarm for the tool pot unclocked |
A0007.5 |
2005 |
Regulation is invalid when feedrate override is fixed to 100% |
A0007.6 |
2006 |
Override on the panel is disabled when external override is enabled |
A0007.7 |
2007 |
Program does not run when external pause switch is OFF |
A0008.0 |
2008 |
Axis does not move when manual override is 0 |
A0008.1 |
2009 |
Disabled feed enabling knob input, fail to operate the program |
A0008.2 |
2010 |
Disabled spindle enabling knob input, fail to rotate the spindle |
A0008.3 |
2011 |
Workpiece number has been reached to the setting numbers |
A0008.4 |
2012 |
Spindle is on the position control, which can not be rotated the spindle. |
|
|
|
|