K1000Mi-A&K1000M4i-A are high cost-performance CNC systems for drilling and milling machine. They adopt new software and hardware design, and 7 inch color LCD display with high resolution.
They provide built-in multifunctional PLC process and rich software control functions. They can control 3/4 feeding axes, 3/4 simultaneously controlled axes.
They can be matched with KND Digital AC servo driver. K1000Mi-A&K1000M4i-A are suitable for CNC Drilling,
l Equipped with a 7 inches TFT color LCD with the resolution of 800×480.
l Be able to process up to 1000 blocks of program per second, which makes the high-speed & mini-line cutting available.
l Input and output signals’ points can be extended up to 512/512 by CAN bus.
l The rapid traverse rate reaches up to 60 m/min and the feed rate reaches up to 30 m/min.
l Support tools regulation instrument and provide a wealth of tool regulation functions such as the rectangle center tool regulation function, the circle center tool regulation function etc.
l Equipped with U-disk port through which CNC systems provide the following functions: store and recover systems’ software and machining data, perform DNC machining by executing a program in U-disks.
l Provide a wealth of software control functions such as the macro-B function, the additional workpiece coordinate system function, the helical interpolation function and so on.
l Provide a wealth of system control functions such as the high-speed & high-precision function, the time-limitation function, the pitch-error and backlash compensation functions, the function of executing multi-blocks of commands in MDI mode, the function of protecting parameters & programs and so on.
l Support the function of servo spindles, which makes the spindle orienting function and the rigid tapping function available.
Item
|
Specification
|
Model
|
K1000Mi-A
|
K1000M4i-A
|
Controlled axis number
|
3 (X, Y, Z)
|
4 (X, Y, Z,4)
|
Simultaneously controlled axis number
|
3
|
4
|
Interpolation
|
Linear, arc, helix, polar coordinate(optional)
|
Least command unit
|
0.001mm or 0.0001inch
|
Maximum command
|
±99999.999 mm
|
Rapid traverse rate
|
60000 mm/min
|
Maximum feed rate
|
30000.000 mm/min
|
Override of feed rate
|
0~150%
|
Program memory space, program number, electronic disk number
|
640KB/128/3
|
Screen
|
7 inch TFT
|
800×480, Chinese/English menu
|
Additional operator’s interface
|
Additional operator’s panel
Independent operation box
|
Display
|
Position, machining time, workpiece counter, date, time, speed etc.
|
Graph
|
Parameters setting and paths displaying
|
Tool compensation
|
Tool length compensation
Tool nose radius compensation
|
Type C tool compensation
|
Pitch error compensation
Backlash compensation
|
Supplied
|
Spindle function
|
Gear shifting
Analog spindle control
Rigid taping control
|
Miscellaneous function
|
Spindle CW/CCW/brake control
Lubrication control
Coolant control
Other optional function according to customer’s application
|
Program editing
|
Incremental/absolute/mixed/decimal point programming
|
Workpiece coordinate system
|
G54~G59
|
Subprogram calling
|
Supplied
|
Metric/inch programming
|
Supplied
|
Communication function
|
RS232 serial port (baud rate reaches up to 115200 bps)
|
Remote control
|
Transmit machining programs
|
U-disk
|
Supplied
|
Macro programming
|
Macro A or Macro B
|
Emergency stop
Stroke limitation check
|
Support up to 3 emergency stop signals
Stored stroke limitation check
Hardware stroke limitation check
|
Alarm
|
P/S alarm, driver alarm, overtravel alarm, system error alarm, external alarm etc.
|
Acc./dec. control
|
Linear and exponential
|
Reference position returning
|
Automatic
Manual
|
Electronic gear ratio
|
1~65535/1~65535
|
Machine control
|
Machine lock
Feed hold
Optional block skip
|
Feed control
|
Automatic, manual, step, hand wheel
|
I/O point number
|
DI:40
DO:24
I/O point number can be extended up to 512/512 using CAN bus
|
Driver
|
Digit AC servo driver
|
Tool offset number
|
32
|
Tool rest control
|
By PLC process
|
Drilling/taping/boring cycles
|
Supplied
|
Plant specifying
|
G17/G18/G19
|
DNC
|
RS232 or U-disk
|
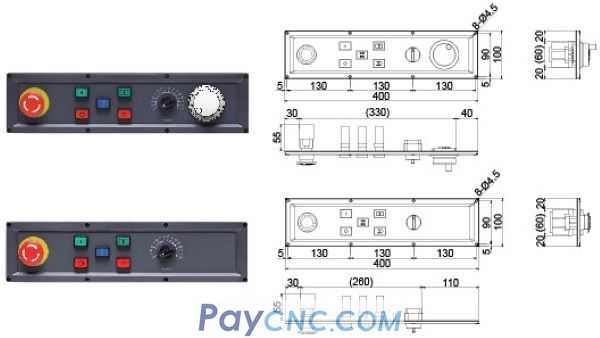
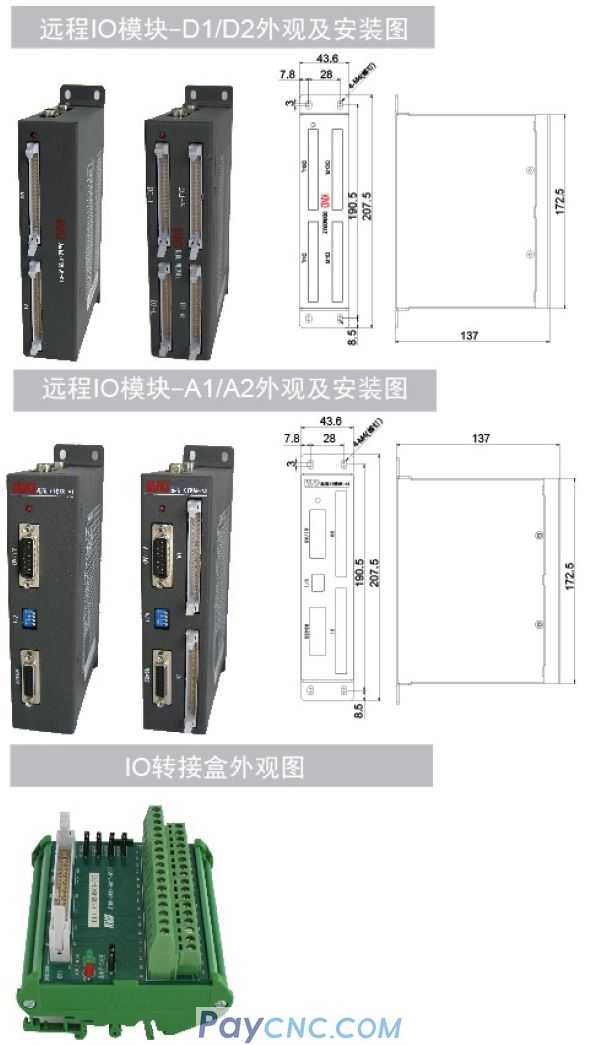
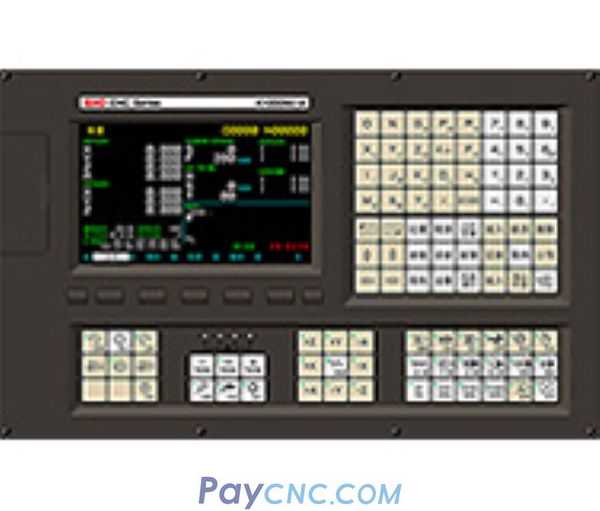 |