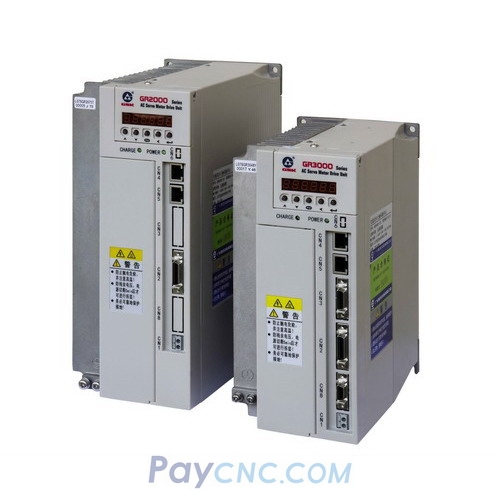
1. Machine tool servo drive parameters
The drive parameters of the transmission system of machine tools (lathes, milling machines, etc.) are composed of the main transmission drive system parameters and the feed drive system drive parameters. In order to meet the corresponding processing requirements, the drive motor of the main transmission or feed drive system should have a certain power and speed range. Usually, the drive power of the motor (including the spindle motor and the feed motor) is called the power parameter; its speed and speed range are called motion parameters.
2 Calculation of power parameters
2.1 Calculation of main transmission drive power
The main transmission power P is the main basis for selecting the main motor and calculating the strength of machine tool parts and structures. The main transmission power P can be determined based on the cutting power and the main transmission efficiency η, that is:
The total efficiency of the main transmission can generally be taken as η=0.7~0.85. When the main transmission chain is long, the loss is large and the transmission efficiency is low, so a smaller value can be taken; when the main transmission chain is short, the loss is small and the transmission efficiency is high, so a larger value can be taken. In formula (1), the cutting power can be calculated according to the following formula after selecting a representative cutting amount (machine tool design standard or user requirement): Where: - main cutting force (N); v - cutting speed (m/min); M - cutting torque (N·m); n - spindle speed (r/min).
2.2 Calculation of feed transmission drive power The feed transmission drive power includes two parts: feed transmission power and idle rapid movement power. When calculating the feed power, it can be determined based on the feed force F, feed speed v, and mechanical efficiency, that is: Where, the mechanical efficiency is 0.15~0.2, and the feed force is calculated based on the guide rail form used in the machine tool design. When calculating the power of fast moving in idle stroke, it can be calculated according to the inertia force and transmission friction force of moving parts such as worktable or slide tool holder, the formula is: Where: --Safety factor, value 1.5~2.5 (determined by safety index); M--Torque required to overcome inertia force (N·m); n-Motor speed (r/min); W-Weight of moving parts (N); f-Friction coefficient between moving parts and guide rails, value 0.15~0.2; --Fast moving speed (m/min), determined according to machine tool design index; η-Mechanical efficiency, value 0.15~0.2.
3 Motion parameters and their ranges
3.1 Main drive limit speed and speed range For machine tools with rotary motion as the main drive, in order to adapt to the changes in cutting speed v and workpiece (tool) diameter d, the minimum and maximum speeds of the spindle can be determined according to the following formula: Where: --Minimum processing diameter (mm); --Maximum processing diameter (mm); --Minimum cutting speed (m/min); --Maximum cutting speed (m/min). In the main drive, the ratio of the highest speed to the lowest speed is called the speed range, that is: When designing a machine tool, the speed range should be determined by considering both the process requirements and the development trend of cutting processing. If the speed range is too large, the design and manufacturing cost of the machine tool will be high; if the speed range is too small, the versatility of the machine tool will not be high.
3.2 Feed drive speed and speed range The speed of the feed drive drive motor is determined by the working feed speed of the machine tool table or tool holder and the fast moving speed of the idle stroke. When the motor is directly connected to the screw, the machine tool table (tool holder) is driven by the screw nut transmission mechanism, then the motor speed should meet the following requirements: Where: -- Table fast feed speed (mm/min); -- Screw lead (mm). If there is a reduction mechanism between the motor and the screw, then: Where: i—transmission ratio of the reduction mechanism; If the motor drives the rotary table to rotate through the worm gear reduction mechanism, then: Where: i—transmission ratio from the motor to the rotary table; —fast forward speed of the rotary table (r/min) It can be seen that the selection of motor speed is related to the design of the mechanical transmission mechanism. The speed regulation range of the motor depends on the minimum feed amount and the maximum speed of rapid movement of the machine tool processing.
4 Summary The shape and size of each component of the machine tool transmission system are determined according to its power parameters, and the process range of the machine tool is determined by the motion parameters. Therefore, the theoretical calculation results of these parameters provide an important basis for the reasonable design of the machine tool. However, the processing range of the machine tool is wide and the processing conditions are changeable. In order to more accurately select the power parameters and motion parameters, in addition to using theoretical calculation methods to determine, analogy, testing and other methods should also be used to compare and determine. |