Fanuc Spindle Amplifier Fault
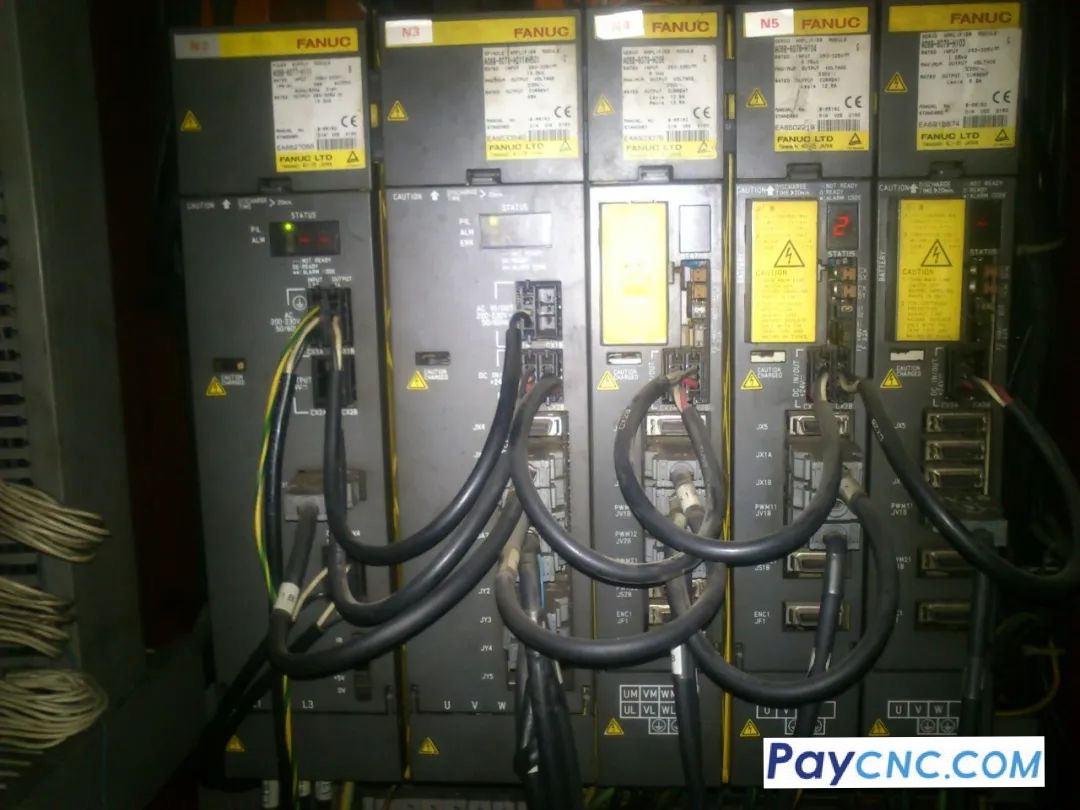
Treatment of common faults in the spindle servo system
1) Faults and diagnosis of DC spindle servo system
(1) The spindle does not rotate. The causes of this fault are:
① The printed circuit board is too dirty;
② The trigger pulse circuit fails and no pulse is generated;
③ The spindle motor power line is broken or the servo control unit is poorly connected;
④ The high/low gear switching clutch is not switched normally;
⑤ The machine tool is too loaded;
⑥ The machine tool does not give the spindle rotation signal.
(2) The spindle motor vibrates or makes too much noise. The causes of this type of fault are:
① The system power supply is missing a phase or the power supply voltage is abnormal;
② The power supply frequency switch (50/60HZ switching) on the spindle control unit is set incorrectly;
③ The gain circuit and the tremor circuit on the servo unit are improperly adjusted;
④ The current feedback circuit is not adjusted properly;
⑤ The phase sequence of the power supply is incorrect;
⑥ Motor bearing failure;
⑦ The spindle gear is not meshing well or the spindle load is too large.
(3) The spindle motor speed is abnormal. The causes of this fault are:
① D/A (digital/analog) converter failure;
② Tachometer generator failure;
③ Speed command error;
④ Motor failure, overload, printed circuit board failure.
(4) Overcurrent alarm occurs. Possible causes of overcurrent include: current limit setting error, synchronous pulse disorder; internal short circuit of the spindle motor electrode coil; +15V power supply abnormality.
2) AC spindle servo system failure and diagnosis
(1) The motor does not rotate or does not reach the normal speed. The causes of this type of fault are:
① The speed command is abnormal. If there is an alarm, it can be handled according to the alarm content;
② The spindle motor cannot start (may be related to the sensor used for spindle orientation control).
(2) The fuse of the AC input circuit is blown. The causes of this type of fault are mostly:
① The impedance of the AC power supply side is too high (for example, an autotransformer is used instead of an isolation transformer on the power supply side);
② The surge absorber at the AC power supply input is damaged;
③ The power rectifier bridge is damaged;
④ The transistor module used in the inverter is damaged or the printed circuit board of the control unit is faulty.
(3) The fuse of the regeneration circuit is blown. This is mostly caused by the acceleration or deceleration frequency of the spindle motor being too high.
(4) The motor is overheated. Possible causes of overheating include:
① Excessive load;
② The fan inside the motor is damaged;
③ Poor connection between the motor and the control unit, etc.
(5) The spindle motor has abnormal noise and vibration. At this time, it should be analyzed: If it occurs during the deceleration process, the fault occurs in the regeneration circuit. Check whether the fuse in the circuit is blown and whether the transistor is damaged. If it occurs at a constant speed, check whether the feedback voltage is normal. |