|
|
|
GSK988T CNC Alarm List
GSK988T CNC Alarm List
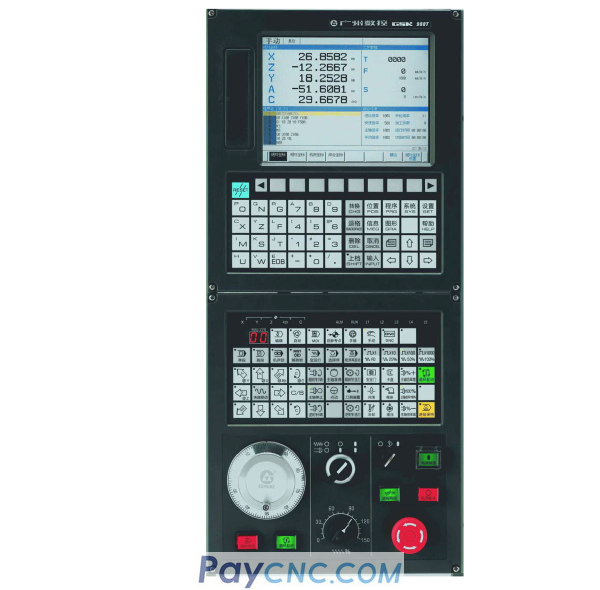
No. |
Message |
Content |
0000 |
Emergency stop, ESP open
circuit |
Recover ESP signal input to clear alarm. |
|
|
|
001 |
Program open failure |
Press reset key to clear alam or power on after
power off. |
002 |
One block cannot exceed 256
characters |
Modify the program because of too many characters
in it. |
003 |
Data exceeds the permitted
range |
Data input exceeds the permitted range or the
specified data exceeds 8 numbers. Modifty the data. |
004 |
Addresss not found |
Only input numerical value or sign instead of
address at the head of the block. Modity the
program. |
005 |
No data fllowing addresses |
Data does not follow the address or the expression
followed the address is mistaken without brackets.
Modify the program. |
006 |
Incorrect negative sign |
Sign"-" is used by mistake( use it in mistaken
position or input them too many). Modity the
program. |
007 |
Incorrectly used decimal point |
The decimal point " is used by mistake( use itin
mistaken position or input them too many). Modity
the program. |
008 |
llegal address input |
The unavailable addresses are input in the valid
message area. Modify the program. |
009 |
Incorrect G code |
An unusable G code or G code correspondingtoa
not provided function is specifed. Modify the
program. |
010 |
Address duplication error |
The same addressed appears more than once in a
block. Alternatively, a block contains two or moreG
codes belonging to the same group. Please referto
parameter 3403#6AD2. Modity the program. |
575 |
011 |
Command cannot run in DNC
occurs |
Command that cannot run in DNC is found. Modify
the program. |
012 |
Too many M codes |
Specifying multiple M codes in the same block is not
allowed. Please refer to parameter 3404#7 M3B.
Modify the program. |
014 |
Divided by zero |
Division by zero is specified (including tan 90°).
Modify the program. |
017 |
Parameter writing failure |
Please check whether the parameter file is in
normal state. Pay attention that the user area may
be corrupted. |
018 |
Part program operation failure |
Press "RESET" key to cancel the alarm. |
019 |
End of record |
The end of record (%) is specifed, or the program
end is not specified. Please refer to parameter
3404#6 EOR. Modify the program. |
020 |
DNC time out |
DNC transmission failure; Please checkit. |
021 |
The setting value of feedrate is
not within the range. |
During cutting feed, the feedrate is not specified or
incorrectly specified. The values for modal G98 and
G99 are different. Please check modal G98 and
G99, and modify the program. |
022 |
The setting value of spindle
speed is outof the range. |
Spindle rotational speed or surface speed is set
incorretly. Please refer to parameter 3031 SCB and
modify the program. |
023 |
M command value is out of the
range. |
A wrong M code is specified. Please refer to
parameter 3030 MCB and modify the program. |
024 |
G code usage error |
The G code needs to be used independently, and
cannot coexist with other G codes in the same
block. Modify the program. |
025 |
Illegal tool number |
An inexistent tool number is specified. Please refer
to parameter 3032 TCB and modifty the program. |
028 |
T code is not allowed in this
block. |
G50, G10 and G04 cannot be specified in the same
block with T codes. Please refer to parameter
5006#1 TGC and modify the program. |
031 |
Too many axes commanded |
The number of commanded axes exceeds that of
simultaneously controlled axes. Modify the program. |
032 |
Axis that cannot perform |
Axis not included in the selected plane is specified |
|
|
interpolation command is
specified. |
or the basic axis and the parallel axis are specifed
simultaneously. Modity the program. |
033 |
llegal plane axis commanded |
In circular interpolation, axis not included in the
selected plane is specifed. Modify the program. |
034 |
No arc radius command |
In circular interpolation, neither R nor 1, J, K is
specified. Refer to parameter 3403#5 CIR and
modify the program. |
035 |
Illegal radius command |
In circular interpolation, address R value is wrong.
Please refer to parameter 3403#4 RER and modify
the program. |
036 |
Exceeds the radius difference
range |
In circular interpolation, the difference between the
distance from the start point to the center point and
distance from the end point to the center point
exceeds the value set by parameter. Please refer to
parameter and modify the program. |
037 |
Thread run-out length J, K value
commanded incorrectly in thread
cutting. |
The run-out length exceeds the ermitted range. K
value is less than zero in G32, G34 commands; J
value or K value is less than zero in G92 command.
Modify the program. |
038 |
llegal lead command |
Lead command value F is out of the range; or in
variable lead thread cutting, the lead variation
exceeds the range. Modify the program. |
039 |
In thread cutting command, the
thread run-out length of long axis
is excessive. |
The thread run-out length of long axis exceeds the
thread cutting length. Modify the program. |
040 |
In thread cutting command, the
thread run-out length of short
axis is excessive. |
In G92 command, the thread run-out length of the
short axis exceeds the distance from the starting
point to the end point. |
041 |
Illegal plane selection |
In plane selection command, more than one parallel
axes are specified in the same direction. Modify the
program. |
042 |
Metric/inch conversion
command error |
The metric/inch conversion command is not
specified alone in a line, or is not specified in the
first line. Metric/inch conversion is performed when
a subprogram is called. Modify the program. |
047 |
The specifed axis does not |
The specified axis does not return to the reference |
|
return to the reference point. |
point by cycle start. Please perform reference point
return. |
048 |
Wrong reference point
commanded |
In G30 block, a value other than 2~4 is specified by
P. Modity the program. |
058 |
G31 cannot be used in
feed-per-rotation mode |
In feed-per-rotation mode, skip cutting commandis
specified. Modify the program. |
059 |
G31 cannot be used in tool nose
radius compensation mode |
Skip cutting command is specified in tool nose
radius compensation mode. Modify the program. |
065 |
The offset value are accumulated
excessively |
In G50 offset accumulation, the accumulated offset
exceeds the permitted range. Modify the program. |
074 |
llegal command G12.1/G13.1 |
When the polar coordinate interpolation is startedor
cancelled, the condition is wrong. 1). G12.1/G13.1
is specified in the mode that is not specified by G40.
2). Error is found in plane selection. The parameter
specifing is erroneous. Modify the programor the
parameter. |
075 |
An unusable G code is specified
in polar coordinate interpolation. |
An unusable G code is specified in polar coordinate
interpolation. Modify the program. |
081 |
Undefined address P |
In the programs commanded by M98, G65, G66, the
address P (program number) is not defined. Modify
the program. |
082 |
Subprogram nesting error |
The nested subprogram exceeds 12 levels. |
083 |
Program number not found |
In the blocks that contain M98, M99, G65, G66, the
program number specified by address P is not
found. Modify the program. |
084 |
Subprogram call error |
A higher-level program or the subprogram itselfis
called by M98, G66 or G66. Modify the program. |
085 |
Program call statement cannot
be run in MDI and DNC modes. |
Macro program call and subprogram call in MDI and
DNC modes are not suppoted. Modify the program. |
090 |
Axis command error in spindle
constant surface speed control
mode |
In modal G96, the basic calculation axis
commanded by parameter does not exist. Modify
the program. |
121 |
Canned cycle command is
specified in non-ZX plane. |
The canned cycle command is not specified in the
basic ZX coordinate system. Modify the program. |
122 |
Axis not included in the basicZX |
Axis not included in the ZX coordinate system is |
|
|
coordinate system is specified in
canned cycle. |
specified in canned cycle. Modify the program. |
123 |
The R value (radius value) is
greater than the U value
(absolute value) in G90, G92
commands. |
In G90, G92 commands, when the plus or minus
signs for the R and U are different, the absolute
value of R value (radius value) is greater the U
value (absolute value). Modify the program. |
124 |
In G94 command, the R absolute
value is greater than W absolute
value |
In G94 command, when the plus or minus signs for
the R and W are different, the absolute valueofRis
greater that of the W value. Modify the program. |
126 |
Illegal plane selection in
multiple-cycle command |
Cycle command is not specified in ZX plane. Modify
the program. |
127 |
Axis not included in the ZX plane
is specified in G70~G76. |
Axis not included in the ZX plane is specified in
G70~G76 commands or the G70~G76 loop. Modify
the program. |
128 |
Incorrect G code in G70~G73 |
An unusable G code is commanded between the
two blocks which is specified by addresses P andQ
in G70~G73. Modify the program. |
129 |
G70~G73 commands cannot be
run in MDI mode |
G70~G73 commands including addresses P, Q are
specified in MDI mode. |
130 |
Macro statement execution is not
allowed in G70~G73 loop |
Macro statement execution is not allowed in
G70~G73 loop. Modify the program. |
131 |
Subprogram is called in
G70~G73 loop |
Subprogram cannot be called in G70~G73 loop.
Modify the program. |
132 |
Subprogram is called in
G70~G73 command lines |
Subprogram cannot be called in G70~G73
command lines. Modify the program. |
133 |
In G70~G73 commands, the
addresses P or Q is out of the
range |
In G70~G73 commands, the addresses P or Q is
undefined or out of the range. Modify the program. |
134 |
The sequence number is not
found in G70~G73 commands |
The sequence number specified by addressPorQ
is not found in G70~G73 commands. Modify the
program. |
135 |
P and Q commands error in
G70~G73 commands |
In G70~G73 commands, the command valuesofP
and Q are the same. Modify the program. |
136 Two continuous blocks is not Two continuous blocks is not found in G71~G73
found in G71~G73 commands commands, which will cause error. Modify the
program. |
137 |
In G71~G73 commands, the
number of Ns~Nf blocks exceeds
100. |
In G71~G73 commands, the Ns-Nf blocks are
excessive. Modify the program. |
138 |
In G71~G73 commands, the
Ns-Nf blocks are non-monotonic |
In multiple cycle command (G71 or G72), a
non-monotonic object structure is defined; or in G73
cycle, the Z axis is non-monotonic; when theZ axis
is set with retract amount or finishing allowance, the
X axis is non-monotonic. Please refer to
parameter 5102#1 MRC and modify the program. |
139 |
The positioning point
commanded by G71~G73is
within the cutting range |
When the positioning point commanded by
G71~G73 is within the cutting range, tool ollision
may occur. Please refer to parameter 5104#2 FCK
and modify the program. |
141 |
In G73 cycle, the tool retract
direction of X axis is inconsistent
with the finishing allowance
direction. |
In G73 cycle, the tool retract direction of X axis is
opposite to the finishing allowance direction. Modify
the program. |
142 |
In G73 cycle, the tool retract
direction of Z axis is inconsistent
with the finishing allowance
direction. |
In G73 cycle, the tool retract direction of Z axis is
opposite to the finishing allowance direction. Modify
the program. |
144 |
GO or G01 is not commandedin
starting block of the G71~G72
loop. |
G0O or G01 needs to be commanded in starting
block of the G71~G72 loop. Modify the program. |
145 |
None of G00-G03 is commanded
in starting block of the G73 loop |
G0O, G01, G02 or G03 is not commanded in the
starting block of the G73 loop. Modify the program. |
146 |
Only X axis increment is needed
in the starting block of G71 loop |
X axis is not commanded in the starting block of the
G71 loop, or the X axis increment is zero, or Z axis
is commanded. Modify the program. |
147 |
Only Z axis increment is needed
in the starting block of G72 loop |
Z axis is not commanded in the starting block of the
G71 loop, or the Z axis increment is zero, or X axis
is commanded. Modify the program. |
148 |
The single feeding amount in
G71 or G72 command is less
than zero |
The single feeding amount in G71 or G72 command
is less than zero. Modify the program. |
149 |
The single tool retracting amount |
The single retracting amount R(e)in G71 or G72 |
|
R(e)inG71 on G72 commandis
less than zero |
command is less than zero. Modify the program. |
151 |
The number of repetition R(d) in
G73 command is out of the
permitted range |
The number of repetition R(d) in G73 commandis
less than 1 or greater than 000 ater rounding.
Modify the program. |
156 |
R(e) is less than zeroin G74or
G75 command |
Single tool retracting amount R(e) is less than zero
in G74 or G75 command. Modify the program. |
157 |
R(Od) is less than zeroin G74or
G75 command |
The tool retracting amount R(Od) is less than zero
in G74 or G75 command when the cutting feed
reaches the end point. Modify the program. |
161 |
The repetitin number of G76is
less than 1 or greater than 99 |
The repetition number of G76 is less than 1 or
greater than 99. Modify the program. |
165 |
The G76 finishing alowance R(d)
exceeds the permitted range |
The G76 finishing allowance R(d) is less than a
minimum increment. Modify the program. |
166 |
During taper thread ctting
commanded by G76, the R value
and U value are unmatched |
During taper thread cuting commanded byG76, the
start point of machining is between the thread start
point and thread end point. Modify the program. |
167 |
Thread height P value is not
specified in G76 command |
Thread height P value is not specified in G76
command. Modify the program. |
168 |
The G76 thread height is less
than the finishing allowance or
the minimum cutting amount |
The G76 thread height is less than the finishing
allowance or the minimum cutting amount. Modify
the program. |
169 |
The Q value in G76 commandis
not within the range |
The first cutting depth is not defined in G76
command: the Q value is not within the range or not
input. Modify the program. |
180 |
Illegal S command in rigid
tapping |
The S code in rigid tapping is undefined or outof the
range. Modify the program. |
181 |
Illegal K command in rigid
tapping |
The specified repettion number K value is out of the
range in rigid tapping. Modify the program. |
182 |
Illegal F command in rigid
tapping |
The cutting feedrate value is F is out of the range in
rigid tapping. Please check the modal G98 and G99
and modify the program. |
183 |
Program er in rigid tapping |
The M code and S value is not in the same block in
rigid tapping. Modify the program. |
184 |
Illegal axis operation in rigid
tapping |
A move axis is specified between the M code and
G84 command in rigid tapping. Modify the |
591 |
|
|
program. |
185 |
The spindle cannot perform rigid
tapping |
In rigid tapping, the spindle is not selected. Modify
the parameter. |
186 |
Plane alteration during rigid
tapping |
During rigid tapping, a non-G18 plane is switchedor
the rigid tapping is enabled in non-G18 plane.
Modity the program. |
187 |
Data error in rigid tapping |
The specified distance is too short or too long in
rigid tapping. Modify the program. |
188 |
Data retition in rigid tapping |
The same M code or S code is repeated between M
code and G84 in rigid tapping. Modify the program. |
189 |
M code repetitin in rigid tapping |
In rigid tapping, the M code cannot be in the same
block with the M code which locks C axis in dilling
canned cycle. Modify the program. |
190 |
Servo spindle command occurs
in rigid tapping |
The increment of the servo spindle occurs in
positioning command in rigid tapping. Modify the
program. |
201 |
Incorrect command used in
macro program |
An unusable function is specified in custom macro
program. Modify the program. |
202 |
Format error in macro program |
There is a format error in <Formula>. Modify the
program. |
203 |
llegal variable number is usedin
macro program. |
A value not defined as variable number is
designated in the custom macro. Modify the
program. |
204 |
Macro program call repetition |
M98, G65 or G66 is called in G66 modal state in the
same program. Modify the program. |
205 |
Bracket nesting error |
The number of bracket nesting level exceeds 5.
Modity the program. |
206 |
Illegal operation data |
The argument of SQRT is a negative value; The
arguments of BCD and BIN are negative values, or
the BIN argument value cannot converted to correct
BCD code. Modify the program. |
207 |
Excessive macro program modal
call |
Macro call or macro program modal call nesting
exceeds 4 levels. Modify the program. |
208 |
Branch of macro program cannot
used in DNC and MDI operation |
Branch of macro program is used in DNC and MDI
operation. Modify the program. |
|
209 |
End statement absent |
DO-END is not 1: 1; the END block contains other
illegal command or the branch cannot be madetoa
location within the loop. Modify the program. |
210 |
Limited authority |
Argument assignment cannot be executed in MDIor
DNC mode due to limited authority. Modify the
program. |
211 |
llegal repettion number |
Condition 1Sn≤3 is not fuilldl (n in Don). Modify the
program. |
212 |
NC statement and macro call
statement coexist in the same
block |
NC statement and macro call statement are used
mixedly. Modify the program. |
213 |
Illegal macro sequence number |
The defined sequence number in branch command
is not within 1-~9999, or they cannot by searched.
Modify the program. |
214 |
llegal argument address |
An unallowable address is specified in <argument> .
Modify the program. |
216 |
Illegal argument value |
The argument value is erroneous or ilegal. Modify
the program. |
217 |
Data error in logical operation
command |
The data in logical operation command OR, XOR,
AND are negative values. Modify the program. |
218 |
G67 modal call cancel is
commanded |
When G66 macro modal call is not specifled, G67
modal call cancel is commanded. Check if it is
necessary to write G66 command. Please refer to
parameter 6000#0G67 and modify the program. |
251 |
The intersection point cannot be
determined in tool nose radius
compensation mode |
The intersection point cannot be determined in tool
nose radius compensation mode. Modify the
program. |
252 |
Tool nose radius compensation
mode cannot be set or canceled
in circular interpolation |
Tool nose radius compensation mode is set or
canceled in circular interpolation. Modify the
program. |
253 |
Compensation plane switchingis
not allowed in tool nose radius
compensation |
Compensation plane is changed in tool nose radius
compensation mode. Modify the program. |
254 |
Interference is generated in
circular block in tool nose radius
compensation mode |
In tool nose radius compensation mode, the start
point or end point of an arc is the same with the
center point, or the end point is not on the arc, which |
|
|
may cause overcut. Modify the program. |
255 |
In tool nose radius compensation
mode, interference occurs in G90
or G94 block |
Overcut may occur when tool nose radius
compensation is commanded in G90 or G94 block.
Modify the program. |
256 |
Overcut oCcurs during
interference check in tool nose
radius compensation mode |
The overcut may occur in tool nose radius
compensation mode. Modify the program. |
257 |
The cutter path direction is
diferent with the programmed
path direction in tool nose radius
compensation mode. |
The tool path direction is different with the
programmed path direction in tool nose radius
compensation mode (90°~270° diference). Overcut
may occur. Modify the program. |
258 |
G41 or G42 execution is not
allowed in MDI mode |
G41 or G42 (tool nose radius compensation) is
specified in MDI mode. Please refer to parameter
5008#4 MCR and modify the program. |
259 |
Overcut is produced within the
cutting full circle |
Overcut is produced within the cutting full circle in
tool nose radius compensation mode. Please refer
to parameter 5008#5 CNF and modify the program. |
260 |
Overcut may be produced when
a step less than the tool radiusis
machined |
In tool nose radius compensation mode, overcut
may be produced when a step less than the tool
radius is machined. Please refer to parameter
5008#6 CNS and modify the program. |
261 |
The circular radius is less than
the tool radius when a inner circle
is machined |
In tool nose radius compensation mode, overcut
may occur if the circular radius is less than the tool
radius when an inner circle is machined. Modify the
program. |
262 |
Circular command occurs when
tool nose radius compensationis
temporarily cancelled or set |
In tool nose radius compensation mode, when G
command for which the compensation mode needs
to be temporarily cancelled is specified, circular
command is specified to set or cancel the
compensation mode. Modify the program. |
263 |
Error is found in tool nose radius
compensation mode |
Programming error or operation error is found in tool
nose radius compensation mode. Modify the
program. |
|
|
|
|