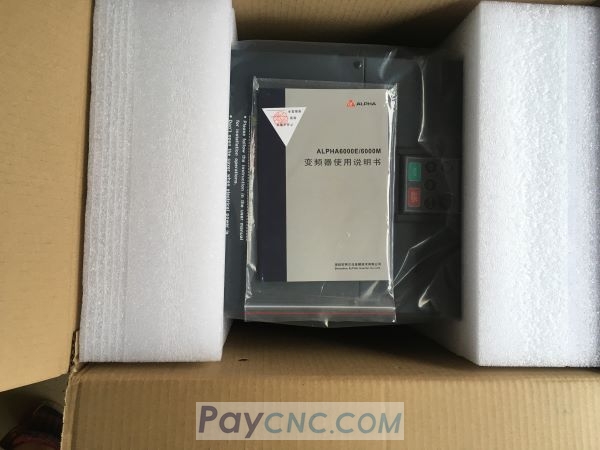
Due to the continuous development and progress of power electronics technology, along with the introduction and improvement of new control theories, AC speed regulation transmission, especially variable frequency speed regulation transmission with excellent performance, has developed rapidly. In recent years, the price of frequency converters has continued to decline, while its use functions have been continuously improved and expanded. It is now widely used in driving from some household appliances of hundreds of watts to some large industrial transmission devices of thousands of kilowatts. AC variable frequency speed regulation has transitioned from the initial speed regulation of fans and pumps to various industrial sites that require high-precision and fast-response high-performance speed regulation indicators. The large-scale promotion and use of frequency converters has achieved remarkable application results in energy saving, labor saving, automation, improving productivity, improving quality, reducing maintenance and improving comfort. However, frequency converters are a new power electronic product that has emerged in the past 20 years and contains a variety of high-tech technologies. In order to make it play a good application effect, it is necessary to conduct in-depth research on its selection and configuration.
2 Selection of frequency converters
The correct selection of frequency converters is crucial to the normal operation of the electronic control system of mechanical equipment. When selecting a frequency converter, we must first consider the type of mechanical equipment, load torque characteristics, speed regulation range, static speed accuracy, starting torque and the requirements of the use environment, and then decide which control mode and protection structure of the frequency converter is most suitable. The so-called suitability means achieving the best cost-effectiveness of the frequency converter application under the premise of meeting the actual process production requirements and use occasions of the mechanical equipment.
2.1 Load torque characteristics of mechanical equipment
In practice, people often divide production machinery into three types according to the different load torque characteristics: constant torque load, constant power load and fluid load.
(1) Constant torque load
In this type of load, the load torque TL is independent of the speed n. TL always remains constant or basically constant at any speed, and the load power increases linearly with the increase of load speed. Friction loads such as conveyor belts, mixers, extruders and feed mechanisms of mechanical equipment, as well as gravity loads such as cranes, hoists and elevators, are all constant torque loads.
When the frequency converter is driving a load with constant torque characteristics, the output torque at low speed must be large enough and have sufficient overload capacity. If it is necessary to run at a low speed for a long time at a steady speed, the heat dissipation capacity of the standard cage asynchronous motor should be considered to avoid excessive temperature rise of the motor.
(2) Constant power load
The characteristic of this type of load is that the required torque TL is roughly inversely proportional to the speed n, but the product, that is, the power, remains approximately constant. The spindle of metal cutting machine tools and rolling mills, papermaking machines, winders and unwinders in film production lines, etc., are all constant power loads.
The constant power property of the load should be within a certain speed variation range. When the speed is very low, due to the limitation of mechanical strength, TL cannot increase infinitely and transform into a constant torque property at low speed. The constant power zone and constant torque zone of the load have a great influence on the selection of the transmission scheme. When the motor is in constant flux speed regulation, the maximum allowable output torque remains unchanged, which belongs to constant torque speed regulation; while in weak magnetic speed regulation, the maximum allowable output torque is inversely proportional to the speed, which belongs to constant power speed regulation. If the constant torque and constant power speed regulation range of the motor is consistent with the constant torque and constant power range of the load, that is, the so-called "matching", the capacity of the motor and the capacity of the inverter are both minimum.
(3) Fluid loads
The torque of this type of load is proportional to the square of the speed, and the power is proportional to the cube of the speed. Various fans, water pumps and oil pumps are typical fluid loads.
Fluid loads can save a lot of energy by adjusting the air volume and flow rate through inverter speed regulation. Since the power demand of fluid loads increases too fast at high speeds, which is proportional to the cube of the load speed, this type of load should not be operated at over-power frequency.
Appendix Performance characteristics of inverter control methods
2.2 Selecting inverters with appropriate control methods according to load characteristics
There are many types of inverters sold on the market now, and their functions are becoming increasingly powerful. The performance of inverters is becoming more and more a determining factor in the quality of speed regulation performance. In addition to the "innate" conditions of the inverter's own manufacturing process, it is also very important to use what kind of control method the inverter uses. The attached table summarizes the performance characteristics of various inverter control methods in recent years.
In summary, different control methods can be used for asynchronous motor frequency conversion control to obtain speed regulation characteristics with different performance characteristics.
2.3 Select the protective structure of the inverter according to the installation environment
The protective structure of the inverter must be adapted to its installation environment, which requires consideration of factors such as ambient temperature, humidity, dust, pH, corrosive gases, etc., which is closely related to whether the inverter can operate long-term, safely and reliably. Most inverter manufacturers can provide the following commonly used protective structures for users to choose from:
(1) Open IP00, which protects the human body from touching the live parts inside the inverter from the front. It is suitable for installation on screens, panels, and racks in electric control cabinets or electrical rooms, especially for concentrated use of multiple inverters, but it has high requirements for the installation environment.
(2) Closed IP20 and IP21, the inverter with this protective structure has an outer cover on all sides and can be mounted on the wall of a building. It is suitable for most indoor installation environments.
(3) Sealed IP40 and IP42, which are suitable for industrial sites with poor environmental conditions.
(4) Sealed IP54 and IP55, which have dust-proof and waterproof protective structures, are suitable for industrial sites with poor environmental conditions, water spray, dust and certain corrosive gases.
For the calculation of the inverter capacity, please refer to reference [1]. Due to space limitations, this article will not be repeated.
3 Key points of the inverter peripheral configuration
(2) A low-voltage circuit breaker and AC contactor with short-circuit and overload protection should be installed between the inverter and the power supply to prevent the accident from expanding when the inverter fails. The emergency stop control of the electric control system should disconnect the AC contactor on the power supply side of the inverter to completely cut off the power supply of the inverter to ensure the safety of equipment and personnel.
(3) The inverter input terminals R, S, T and output terminals U, V, W cannot be connected incorrectly. The input terminals R, S, and T of the inverter are connected to the input terminals of the three-phase rectifier bridge, while the output terminals U, V, and W are connected to the inverter circuit of the three-phase asynchronous motor. If the two are connected incorrectly, the inverter speed regulation cannot be realized at best, the motor will not run, and the inverter will be burned at worst.
(4) In situations where starting and stopping are frequent, do not use the on and off of the main circuit power supply to control the start and stop of the inverter. Use the RUN/STOP key or SF/SR control terminal on the inverter control panel. Because when the inverter is started, the large-capacity electrolytic capacitor of the DC circuit must be charged first. If the inverter is started frequently, it will inevitably cause the current limiting resistor used for capacitor charging to heat up seriously, and at the same time shorten the service life of the large-capacity electrolytic capacitor.
(5) The terminal "N" of the inverter is the low-level end of the intermediate DC circuit. It is strictly forbidden to connect it to the neutral line or the ground in the three-phase four-wire power supply line, otherwise the three-phase rectifier bridge will be damaged by the power supply short circuit and the inverter will be damaged.
(6) Electromagnetic contactors cannot be installed on the output side of the inverter. If they must be installed, the following conditions must be met: If the inverter is running, it is strictly forbidden to switch the electromagnetic contactors on the output side; the contactors must be switched only after the inverter stops outputting. Because if the contactors on the output side are switched when the inverter is outputting normally, a very high overvoltage will be generated at the moment when the contactor contacts are disconnected, which can easily damage the power electronic devices in the inverter. Therefore, to switch the contactors on the output side of the inverter, the power tube of the inverter must be blocked.
(7) When encountering an inverter with a built-in braking unit that requires an external braking resistor, be sure to pay attention to the correct wiring of the braking resistor. The braking resistor must be connected between P and DB, not between P and N, otherwise the three-phase rectifier bridge of the inverter will work at full load when the inverter is not running, causing the inverter to fail to work normally and the braking resistor may also burn out. |