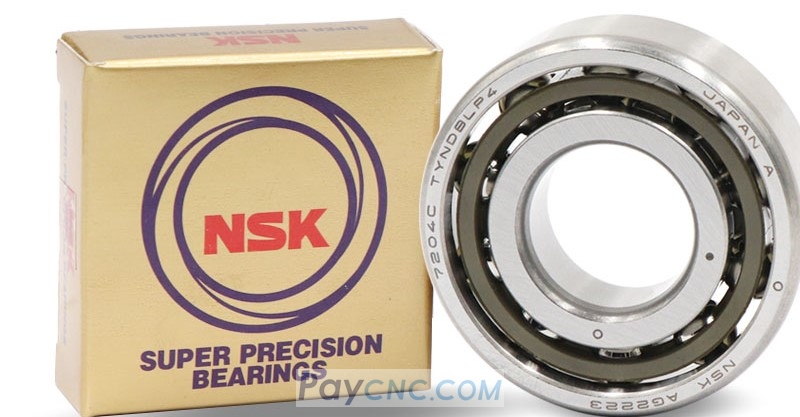
The bearings used in machine tool spindles are divided into two categories: rolling bearings and sliding bearings. From the perspective of rotational accuracy, both types of bearings can meet the requirements, but in terms of their performance indicators, rolling bearings are superior to sliding bearings. The advantages of rolling bearings are: (1) Rolling bearings can work stably under conditions where the speed and load vary greatly. (2) Rolling bearings can work without clearance or even under preload (with a certain amount of interference). (3) The friction coefficient of rolling bearings is small, which helps reduce heat generation. (4) Rolling bearings are easy to lubricate and can be greased. They can be filled once and then replaced until repair. If oil lubrication is used, the amount of oil required per unit time is much smaller than that of sliding bearings. The disadvantages of rolling bearings are: (1) The number of rolling elements is limited, so the radial stiffness of rolling bearings during rotation is variable, which is one of the reasons for vibration. (2) The damping of rolling bearings is low. (3) The radial size of rolling bearings is larger than that of sliding shafts.
In general, machine tools should try to use rolling bearings, especially most vertical spindles, which can be lubricated with grease to avoid oil leakage. Sliding bearings are only used when the roughness of the machining surface is small and the spindle is horizontal, such as cylindrical grinders, surface grinders, high-precision lathes, etc. The precision and stiffness of the bearing directly affect the rotation accuracy of the spindle, which are explained below.
Although rolling bearings have a series of advantages and have been widely used in mechanical equipment, sliding bearings must be used in situations such as high speed, high precision, heavy load, and structural splitting. This is because sliding bearings have some characteristics that rolling bearings cannot replace. Its main advantages are: simple structure, easy manufacturing and assembly and disassembly; good impact resistance and vibration absorption performance, stable operation, high rotation accuracy, and long life. Its main disadvantages are: complex maintenance, high requirements for lubrication conditions, and severe friction and wear when the bearing is in a boundary lubrication state.
Sliding bearings are mainly composed of bearing seats and bushings. According to the direction of the load, they are mainly divided into radial sliding bearings (also known as radial sliding bearings), thrust sliding bearings and radial thrust sliding bearings; according to the lubrication state, they are divided into liquid lubricated bearings, gas lubricated bearings, mixed lubricated bearings, solid lubricated bearings and non-lubricated bearings; according to the load-bearing method, they are divided into lubricated mold load-bearing, direct contact load-bearing and other load-bearing sliding bearings. Bushings are the main parts of sliding bearings. When designing bearings, in addition to selecting suitable bushing materials, the bushing structure should also be reasonably designed, otherwise it will affect the working performance of sliding bearings.
Ordinary sliding bearings are prone to low oil film stiffness, short precision retention period, difficult maintenance, high machining surface roughness, obvious vibration marks, etc. in production due to their own structural factors. Practice has proved that when the spindle sliding bearing is selected as a liquid friction sliding bearing, it has higher precision and stiffness, and the processing quality and productivity can be improved. |