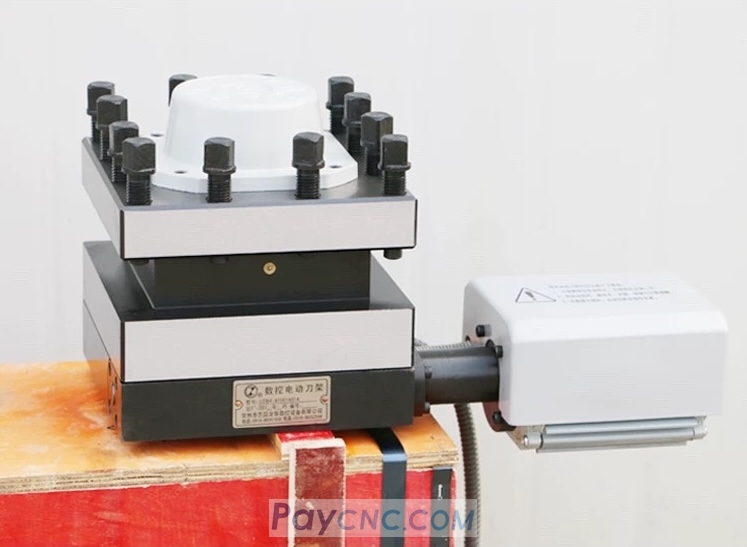
The application of CNC technology and CNC machine tools has successfully solved the automation problem of some medium and small batches of parts with complex shapes and high consistency requirements, which not only greatly improved production efficiency and processing accuracy, but also reduced the labor intensity of workers and shortened the production preparation cycle. However, in the process of using CNC lathes, CNC lathes will inevitably have various faults, so the maintenance of faults has become the most critical issue for CNC lathe users. On the one hand, the after-sales service of the sales company is not The application of CNC technology and CNC machine tools has successfully solved the automation problem of some medium and small batches of parts with complex shapes and high consistency requirements, which not only greatly improved production efficiency and processing accuracy, but also reduced the labor intensity of workers and shortened the production preparation cycle. However, in the process of using CNC lathes, CNC lathes will inevitably have various faults, so the maintenance of faults has become the most critical issue for CNC lathe users. On the one hand, the after-sales service of the sales company cannot be guaranteed in time, and on the other hand, mastering some maintenance techniques can quickly determine the fault, shorten the maintenance time, and make the equipment run as soon as possible. In daily faults, we often encounter faults such as tool holder, spindle, processing, system display, drive, etc. Tool holder faults account for a large proportion of them. Here, we will introduce the various faults of the four-station electric tool holder encountered in daily work and the corresponding solutions, hoping to provide some useful reference for everyone. The CNC system used is the GSK series lathe CNC system produced by Guangzhou CNC Equipment Co., Ltd.
Fault phenomenon 1: The electric tool holder is not locked tightly
Fault cause and treatment method
① The position of the signal disk is not aligned: remove the top cover of the tool holder, rotate and adjust the position of the signal disk, so that the Hall element of the tool holder is aligned with the magnetic steel, so that the tool position stops at the correct position.
② The system anti-lock time is not enough: adjust the system anti-lock time (the new tool holder anti-lock time t = 1.2s).
③ Locking mechanism failure: disassemble the tool holder, adjust the machine, and check whether the positioning pin is broken.
Fault phenomenon 2: a certain tool number of the electric tool holder keeps turning, while the other tool positions can turn
Fault cause and treatment method
① The Hall element of this tool is damaged: confirm which tool position makes the tool holder keep turning, input the rotation of the tool position in the system, and use a multimeter to measure whether the contact of the tool position changes to the +24V contact. If there is no change, it can be determined that the Hall element of the tool position is damaged, and the transmitter or Hall element is replaced
② The signal line of this tool position is broken, causing the system to be unable to detect the position signal: check whether the connection between the tool position signal and the system is broken, and connect it correctly
③ The system's tool position signal receiving circuit has a problem: when it is determined that the Hall element of the tool position is fine, and the connection between the tool position signal and the system is also fine, replace the mainboard |