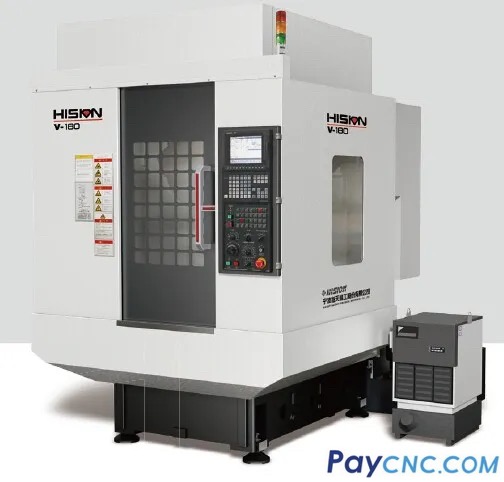
(I) Reverse clearance compensation
In the transmission system of CNC machine tools, the servo motor and the lead screw are usually connected and transmitted in three ways: direct connection, synchronous belt drive, and gear drive. Gears, ball screws, nuts, etc. all have reverse clearance. The existence of this reverse clearance will cause the servo motor to idle when the machine tool table moves in the opposite direction, but the table does not actually move, or the servo motor drives the mechanical part to move but the measuring device does not detect the displacement. For CNC machine tools, the reverse clearance will affect the positioning accuracy and repeat positioning accuracy of the machine tool, thereby affecting the accuracy of the processed products. This requires the CNC system to provide a software compensation function for the reverse clearance, so as to compensate for the reverse clearance of the machine tool, reduce its impact on the accuracy of the machine tool, and improve the accuracy of the processed parts. Often, as the use time of the CNC machine tool increases, the reverse clearance will gradually increase due to the wear of the mechanical part. Therefore, it is necessary to regularly measure and compensate the reverse clearance of each coordinate axis of the CNC machine tool.
(II) Pitch compensation
The linear feed axis on CNC machine tools mostly uses ball screws as mechanical transmission components. The motor drives the ball screw to move, converting the motor's rotational motion into the linear motion of the feed axis. If there is no error between the pitches of the ball screw, the angle of rotation of the ball screw is linearly related to the linear displacement of the corresponding feed axis. However, in practice, there are always errors in the manufacturing process and assembly, and there is a pitch error between the pitches of the ball screw. It is reflected in the linear displacement of the feed axis. There is also a certain error, which will reduce the machining accuracy of the machine tool. Most CNC systems provide the function of pitch error compensation, which can compensate for the pitch error of CNC machine tools to achieve the purpose of reducing machine tool errors and improving machining accuracy. In addition, after a long period of use, due to the different degrees of wear of the pitches of the ball screw, the error between the pitches will be further increased, resulting in a decrease in the machining accuracy of the machine tool. By periodically calibrating and compensating the machine tool, the service life of the machine tool can be extended while maintaining accuracy. |