Cutting fluids are widely used in CNC cutting processes because of their cooling, lubrication, cleaning and rust prevention functions. Cutting fluids often deteriorate, become smelly, corrode, produce foam, and cause skin allergies in operators. The following will share the problems and countermeasures in the use of cutting fluids based on actual work experience.
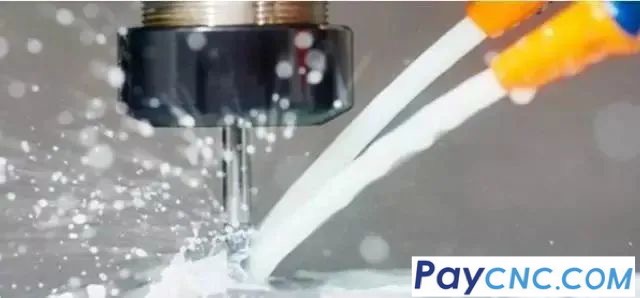
1
Reasons for cutting fluid deterioration and odor - bacteria
(1) Bacteria mainly enter the cutting fluid through the following channels:
1) Bacteria invade during the preparation process, such as bacteria in the water used to prepare the cutting fluid.
2) Bacteria in the air enter the cutting fluid.
3) The transportation of workpieces between processes causes the cutting fluid to be infected.
4) Bad habits of operators, such as littering.
5) Poor cleanliness of machine tools and workshops.
(2) Methods for controlling bacterial growth
1) Use high-quality and stable cutting fluids.
2) Use pure water to prepare concentrated fluids, which is not only easy to prepare, but also can improve the lubricity of the cutting fluid, reduce the amount carried away by chips, and prevent bacterial erosion.
3) When using, the ratio of concentrated liquid in the cutting fluid should not be too low, otherwise it is easy for bacteria to grow.
4) Since the oil used in the machine tool contains bacteria, it is necessary to minimize the mixing of oil leaked from the machine tool into the cutting fluid.
5) When the pH value of the cutting fluid is between 8.3 and 9.2, bacteria are difficult to survive, so new cutting fluid should be added in time to increase the pH value.
6) Keep the cutting fluid clean and do not let the cutting fluid come into contact with dirty oil, food, tobacco and other contaminants.
7) Use disinfectants frequently.
8) Keep the workshop and machine tools clean.
9) If the equipment does not have a filtering device, the floating oil should be skimmed off regularly to remove dirt.
2
Corrosion problems of cutting fluid
(1) Causes of corrosion
1) The proportion of concentrated liquid in the cutting fluid is low.
2) The pH value of the cutting fluid is too high or too low. For example, when the pH is greater than 9.2, it will corrode aluminum. Therefore, the appropriate pH value should be selected according to the metal material.
3) Contact between dissimilar metal materials.
4) Use paper or wood to place workpieces.
5) Stacking parts.
6) The number of bacteria in the cutting fluid exceeds the standard.
7) The humidity of the working environment is too high.
(2) Methods for preventing and controlling corrosion
1) Use pure water to prepare the cutting fluid, and the proportion of the cutting fluid should be used according to the recommended value in the instructions of the cutting fluid used.
2) If necessary, use anti-rust fluid.
3) Control the number of bacteria to avoid the generation of bacteria.
4) Check the humidity and pay attention to controlling the humidity of the working environment within an appropriate range.
5) Avoid contamination of the cutting fluid.
6) Avoid contact between dissimilar materials, such as aluminum and steel, cast iron (containing magnesium) and copper.
3
Problems with foaming
(1) Main causes of foaming
1) The liquid level of the cutting fluid is too low.
2) The flow rate of the cutting fluid is too fast, and the bubbles have no time to overflow, so they accumulate more and more, resulting in a large amount of foaming.
3) There are too many right angles in the water tank design, or the cutting fluid nozzle angle is too straight.
(2) Methods to avoid foaming
1) In the centralized cooling system, the pipelines are connected in series, and the pressure of the pipelines close to the cooling box should be lower.
2) Ensure that the liquid level of the cutting fluid is not too low, check the liquid level in time, and add cutting fluid in time.
3) Control the flow rate of the cutting fluid not too fast.
4) When designing the water tank, pay attention to not having too many right angles in the water tank.
5) When using cutting fluid, pay attention to not having the cutting fluid nozzle angle too straight.
4
Operator skin allergy problem
(1) The main reasons for operator skin allergy
1) The pH value is too high.
2) The composition of the cutting fluid.
3) Insoluble metals and oils used in machine tools.
4) The use ratio of the concentrate is too high.
5) Protective suspension layer on the surface of the cutting fluid, such as odor sealing layer and anti-foaming layer. Bactericide and unclean cutting fluid.
(2) During work, in order to avoid skin allergies of the operator, the following points should be noted:
1) The operator should apply protective oil, wear work clothes and gloves, and should be careful to avoid direct contact between the skin and the cutting fluid.
2) The proportion of concentrate in the cutting fluid must be used according to the recommended value of the cutting fluid.
3) The use of bactericides should be used according to the dosage in the instructions.
In addition, fluororubber and grease rubber are less deformed by cutting fluid and can be given priority when used as machine tool seals. In order to prevent deformation, the fat content of rubber used in machine tool seals should generally be greater than 35%. In addition, in order to effectively prevent the cutting fluid from causing the machine tool paint to fall off, epoxy resin paint or polyurethane paint can be selected.
In short, if you pay attention to the above issues when using cutting fluid in normal production, you can avoid unnecessary economic losses and effectively improve production efficiency. |