Rigid tapping function of FANUC CNC
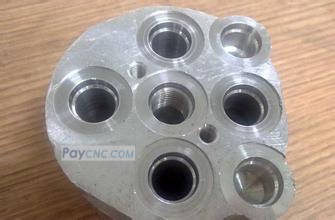
Rigid tapping has become a must-have function on FANUC CNC machining center. It is necessary to debug this function to achieve high-speed, high-efficiency and high-precision performance to meet the wide range of processing needs of users. For deep holes with high precision requirements, it should be achieved by selecting appropriate tapping methods and reasonably setting CNC system parameters.
Rigid tapping of FANUC CNC machining center
Comparison between rigid tapping and ordinary tapping
In ordinary tapping cycles G74/G84 (M series), G84/G88 (T series), the rotation of the spindle and the feed amount of the Z axis are controlled separately, and the acceleration/deceleration of the spindle and the feed axis are also handled independently, so the above conditions cannot be strictly met, especially when the tapping reaches the bottom of the hole, the spindle and the feed axis decelerate to stop, and then accelerate the reverse rotation process, it will be more difficult to meet the above conditions. Therefore, in general, tapping is to improve the accuracy of tapping by installing a flexible spring in the tool sleeve to compensate for the feed of the feed axis. During the rigid tapping cycle, the rotation of the spindle and the feed axis are always synchronized. That is to say, during rigid tapping, the rotation of the spindle must not only achieve speed control, but also position control. The rotation of the spindle and the feed of the tapping axis must achieve linear interpolation, and the acceleration/deceleration during hole bottom processing must still meet the condition of P= F/S (the pitch of the tapping can be directly specified) to improve the accuracy.
Concept and characteristics of rigid tapping
During rigid tapping, the feed rate of the drilling axis corresponding to one rotation of the spindle must be equal to the tapping pitch, that is, the following conditions must be met:
P= F/S
P: tapping pitch (mm)
F: tapping axis feed rate (mm/min)
S: spindle speed (rpm)
Rigid tapping can be completed by any of the following instructions:
(1) _ M29 S _____ The rigid tapping instruction is specified before G74/G84 (M series) or G84/G88 (T series)
(2) _ M29 S _____ The rigid tapping instruction and the tapping instruction G74/G84 (M series) or G84/G88 (T series) are in the same program segment
(3) _ G74/G84 (M series) or G84/G88 (T series) As rigid tapping instruction (use G74/G84
(G84/G88) as rigid tapping instruction or as ordinary tapping instruction can be specified by parameter 5200#0)
Among them, for M series:
G84X_Y_Z_R_P_F_K_; is the standard tapping cycle instruction
G74X_Y_Z_R_P_F_K_; is the reverse thread tapping cycle instruction
For T series:
G84 is the end face rigid tapping cycle (along the Z axis), G88 is the side rigid tapping cycle (along the X axis);
Feed per minute and feed per revolution instructions can be specified in rigid tapping. In feed per minute mode, F / S is the tapping pitch, and in feed per revolution mode, F is the tapping pitch.
For general tapping function, the spindle speed and Z axis feed are independently controlled, so the above conditions may not be met. Especially at the bottom of the hole, the spindle speed and the Z-axis feed decrease and stop, then they reverse and the speed increases. Since they are accelerated and decelerated independently, the above conditions may not be met. For this reason, the feed amount is usually compensated by a spring installed inside the tapping chuck to improve the accuracy of the tapping. This method is called "flexible tapping". If the control spindle rotation and Z-axis feed are always synchronized, the tapping accuracy can be guaranteed. This method is called "rigid tapping". Rigid tapping adds a position encoder to the spindle, feeds back the angular position of the spindle rotation to the control system to form a position closed loop, and establishes a synchronous relationship with the Z-axis feed, so that the linear proportional relationship between the spindle rotation angle and the Z-axis feed size is strictly guaranteed. Because of this synchronous relationship, even if the spindle rotation angle or Z-axis movement position changes due to inertia, different acceleration and deceleration time constants, and load fluctuations do not affect the processing accuracy. If you use rigid tapping to process threaded holes, you can clearly see that when the Z-axis tapping reaches the position, the spindle rotation and the Z-axis feed are decelerated and stopped at the same time, and the spindle reversal and the Z-axis reverse feed are also consistent. It is precisely because of the synchronization relationship that the tap chuck can be an ordinary drill chuck or the simplest special chuck. In addition, when rigid tapping, as long as the tool (tap) strength allows, the spindle speed can be increased a lot, and a spindle speed of 4000r/min is no problem. The processing efficiency is increased by more than 5 times, and the thread accuracy is guaranteed. |