Solutions to the axial movement and radial runout of the spindle of the machining center
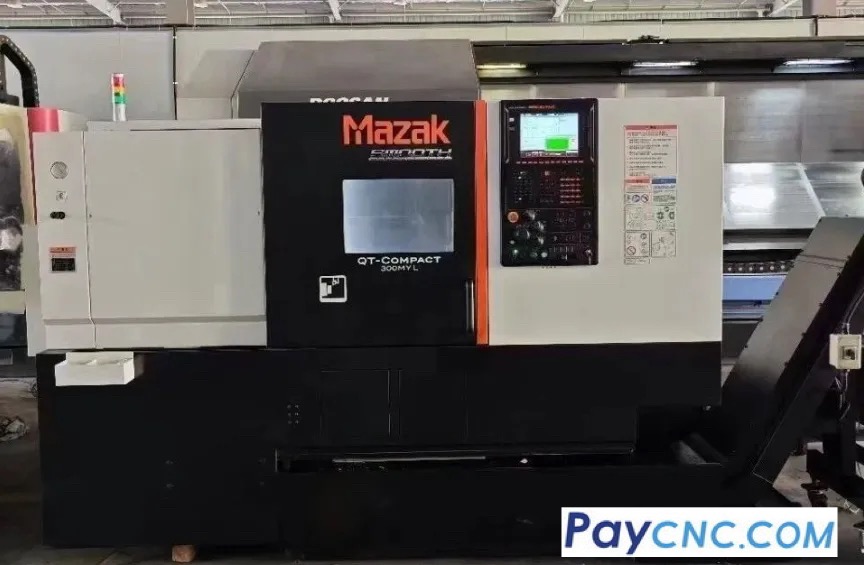
The workpiece processed by the vertical CNC mold machining center has obvious tool drag marks. The surface finish of the workpiece is not high. After increasing the spindle speed and reducing the feed speed, this problem still cannot be solved.
The spindle of the vertical CNC machining center is the executive component of the machine tool. Its function is to support and drive the surface movement of the workpiece or tool. At the same time, it also plays the role of transmitting power and torque, bearing cutting force and driving force and other loads. For the working performance of the spindle component, the rotation accuracy of the spindle main part is one of the important aspects. When the spindle rotates, due to various reasons, the position of its rotation centerline changes with time. If a straight line is used to represent the ideal rotation centerline of the spindle, the offset between the actual rotation centerline and the rotation centerline is called the rotation accuracy of the spindle component. When the CNC mold machining center machine tool is running idle, the size of the longitudinal runout, end face runout and axial runout of the front end of the spindle, and whether the spindle is well assembled will affect the normal operation of the machine tool.
According to the above analysis, the reasons for the axial movement and radial runout of the spindle are roughly as follows:
(1) The spindle bearing is not preloaded properly, causing axial movement or radial runout.
(2) The bearing is seriously damaged, resulting in uneven speed.
(3) The bearing is not properly matched.
According to the listed fault points, you can refer to the following steps to solve the fault.
Step 1: After the CNC mold processing center runs idle for a period of time, touch all the bearings on the spindle with your hand. It is found that the temperature rise is not obvious, and the noise during the processing is small. Therefore, it is ruled out that the fault is caused by serious damage to the bearing itself.
Step 2: Since the preload force of the bearing is adjusted by the manufacturer before leaving the factory, directly replace a pair of new bearings. After installation, it is found that the workpiece processed still has serious drag marks. It can be ruled out that the fault is caused by poor preload of the bearing.
Step 3: After replacing a rear bearing with lower precision, re-operate the machine tool and try to process the workpiece. It is found that the drag marks are significantly improved. It can be concluded that the fault is caused by unreasonable assembly of the bearing. Through calculation, the fault was eliminated after replacing a rear bearing with appropriate accuracy.
Spindle bearings are an important part of the spindle components. The quality of bearing assembly directly affects the radial runout and axial movement accuracy of the rotating shaft. Therefore, to ensure the radial runout and axial movement of the spindle, in addition to requiring the spindle and bearing to have a certain accuracy, the correct assembly method must also be adopted.
The directional assembly of the bearing is essentially based on the error compensation principle, placing the deviation of the center line of the spindle chain hole and the deviation of the front and rear bearings in the same axial section, and assembling in a certain direction to compensate for the error, so as to improve the rotation accuracy of the spindle components. Under the condition that the radial runout of the inner ring of the front and rear bearings and the center line of the spindle taper hole remain unchanged, the radial runout values detected by different assemblies are also different. |