What is cutting? And what are the factors of tool wear?
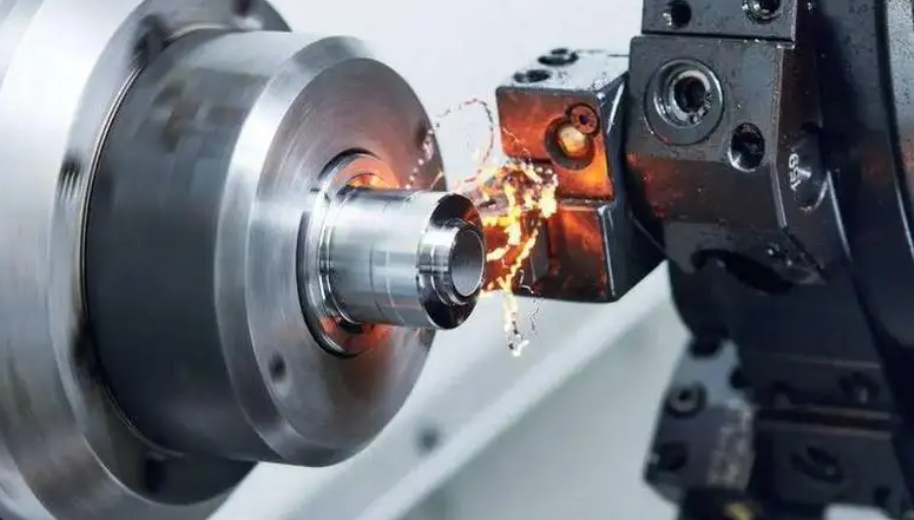
One: What is cutting? Cutting is a processing method that uses cutting tools (including cutting tools, grinding tools and abrasives) to cut off the excess material layer on the blank or workpiece, thereby forming chips, so that the workpiece obtains the specified geometric shape, size and surface quality. Cutting is the main processing method in mechanical manufacturing and is widely used in metal processing, wood processing and other fields. During the cutting process, the tool cuts off the excess material on the surface of the workpiece through relative movement with the workpiece. In this process, the workpiece is cut into by the tool and chips are generated, and a certain cutting force is generated at the same time. Cutting force is an important factor that must be considered in the cutting process. It is closely related to many problems in the cutting field, such as chip flow, processing deformation, thermal stress analysis, tool failure, etc. There are many ways of cutting processing, such as turning, milling, grinding, etc., each of which has its own characteristics and scope of application. Under different cutting methods, the process of the workpiece being cut into by the tool and the cutting force generated will also be different.
In addition, tool wear during cutting is also an inevitable phenomenon. Tool wear will affect processing quality, increase tool consumption, reduce production efficiency and increase processing costs. Therefore, in cutting processing, it is necessary to reasonably select tool materials, cutting amount and cutting fluid, etc. to slow down tool wear and improve processing efficiency. In general, cutting is an important processing method, which is widely used in mechanical manufacturing and industrial production. Through reasonable cutting process and tool selection, efficient and precise processing can be achieved to improve product quality and production efficiency.
2: What are the factors of tool wear? Tool wear is an inevitable phenomenon in cutting processing, and its wear factors are complex and diverse, mainly including the following aspects: 1. Cutting conditions
① Cutting speed: Cutting speed is an important factor affecting tool wear. Excessive cutting speed will lead to increased cutting temperature, thereby accelerating tool wear. Especially when the cutting temperature reaches or exceeds the phase change temperature of the tool material, it will cause phase change wear, significantly reducing the hardness and wear resistance of the tool.
② Feed rate: The size of the feed rate will also affect the wear of the tool. Too little feed rate may increase the cutting force, thereby aggravating the wear of the tool; while too much feed rate may cause the tool to bear too much cutting impact force, resulting in damage or fracture.
③ Cutting depth: Cutting depth also has a certain influence on tool wear. When the cutting depth is too large, the tool needs to bear greater cutting force, thereby accelerating wear.
2. Workpiece material
① Material hardness: The higher the hardness of the workpiece material, the greater the cutting force on the tool during cutting, and the faster the wear.
② Hard points in the material: Hard points in the workpiece material (such as carbides, nitrides, etc.) will scratch the tool surface during the cutting process, resulting in abrasive wear.
③ Material viscosity and plasticity: When processing materials with high viscosity or plasticity, chips are easily accumulated on the top of the blade to form built-up edge, resulting in increased tool wear.
3. Tool material
① Hardness and toughness of tool material: The hardness and toughness of tool material are the key factors that determine its wear resistance. The higher the hardness, the better the wear resistance is usually, but too high hardness may lead to reduced toughness and brittle material.
②Chemical composition of tool materials: At high temperatures, the chemical elements of tool materials and workpiece materials may diffuse with each other, change the composition structure of the tool, reduce its strength and hardness, and thus accelerate wear.
4. Cutting fluid Cutting fluid plays a role of cooling, lubrication and cleaning during the cutting process. Reasonable use of cutting fluid can reduce cutting temperature and reduce friction and wear between the tool and the workpiece. However, if the cutting fluid is used improperly or of poor quality, it may aggravate tool wear.
5. Other factors
① Tool geometry: The geometry of the tool (such as rake angle, back angle, blade inclination angle, etc.) will affect the cutting force and cutting temperature distribution during the cutting process, thereby affecting tool wear.
②Cutting vibration: The vibration during the cutting process will intensify the friction and impact between the tool and the workpiece, thereby accelerating tool wear.
③Tool grinding quality: The quality of tool grinding directly affects its cutting performance and wear resistance. Poor grinding quality will lead to increased tool cutting force, increased cutting temperature and increased wear. In summary, tool wear is the result of the combined effect of multiple factors. In actual cutting processing, it is necessary to select appropriate cutting conditions, workpiece materials, tool materials and cutting fluids according to the specific situation to slow down tool wear and improve processing efficiency and quality.
So what other elements do you know? |