What are the methods to solve the cutting vibration of the five-axis machining center?
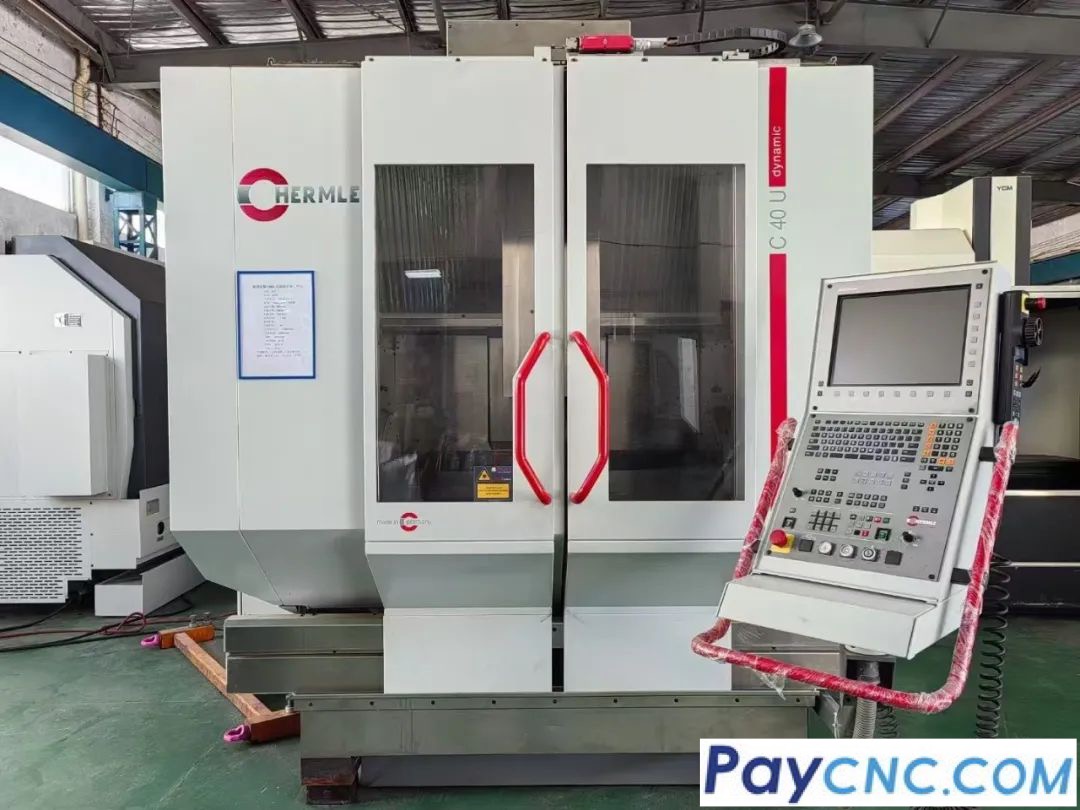
The five-axis machining center is a modern CNC equipment machining center, which is not only suitable for machining complex parts of plates, plates, molds and small housings, but also can complete milling, drilling, drilling, attacking threads and cutting threads.
During the machining process, cutting vibration is an inevitable situation in the machining process of five-axis CNC machine tools, and it is a vibration phenomenon generated during the cutting process. In fact, reasonable cutting vibration has little effect on the machining quality, but once the cutting vibration increases, the amplitude will exceed tens of μm. The violent vibration is usually accompanied by a lot of noise.
If the vibration of the five-axis machining center during the cutting process may exceed 100μm, at this time, the tool or workpiece is in danger of loosening. 100μM is usually regarded as the standard for judging whether the cutting vibration is reasonable. The cutting amplitude exceeds 100μm and cannot continue to be processed. When the amplitude is below 100μm, although it can be processed, the machining surface will leave obvious vibration scratches, and the surface finishing is not allowed. Therefore, the cutting vibration should be limited to a reasonable range.
The following are ways to solve the cutting vibration of the five-axis machining center:
1. Reasonable arrangement of the tool path Reasonable arrangement of the tool path of the five-axis CNC machining center is very important for cutting processing. Milling can be divided into forward milling and reverse milling. Whether it is forward milling or reverse milling, as long as the direction of the milling force is consistent with the clamping direction of the workpiece, it is beneficial to eliminate the vibration of the bent plate parts. Current milling equipment, such as CNC milling machines and five-axis machining centers, are equipped with ball or roller screws, which is very helpful in eliminating vibration during cutting.
2. Reasonable cutting When the five-axis machining center CNC machine tool uses a slender rod end mill to mill deep cavities, the plunge milling method is often used. Plunge milling refers to the axial feeding of the tool like a drill bit. When milling deep cavities, the diameter of the long rod is usually greater than 3 times. It is recommended to use the plunge milling method with axial feeding. Adjusting the cutting parameters is only effective for situations where the cutting vibration is not serious.
The general adjustment method is as follows:
Reduce the rotation speed of the tool or workpiece, reduce the cutting depth, and increase the amount of tooth bending per revolution of the tool or the milling cutter. If vibration occurs during internal thread turning, the feed steps to complete thread turning can be reduced by 112 cuts.
In addition, use a blade with a positive rake angle and a large clearance angle, and equipped with a light chip groove. During filing or milling, this blade has the smallest cutting wedge angle and the lightest cutting speed.
At the same time, using a sharp blade can reduce the cutting force of the CNC machine tool. The timely grinding of the tool and the stability of the processing environment ground are processing conditions that cannot be ignored. |