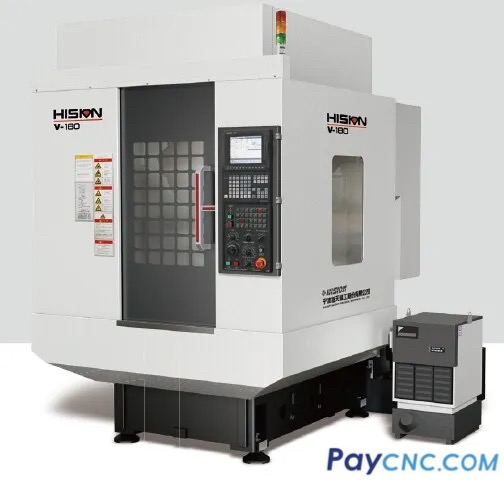
Through the study of CNC machine tool hydraulic systems, it can be found that the main factors that cause vibration and noise in hydraulic systems are as follows:
First, parts are unbalanced, eccentric or improperly adjusted. First, due to the influence of parts imbalance, hydraulic systems, especially motors, etc., often cause bending vibrations due to improper design and manufacturing under the influence of rapid operation. The resulting vibration will spread to other components through the base, which will not only cause vibration, but also bring certain noise. Secondly, improper installation of parts. When installing hydraulic systems, noise is often caused by lack of fairness in component installation. Finally, improper coupling will cause noise. In the hydraulic system of CNC machine tools, the coupling plays a connecting role and is an indispensable part of the connection between the hydraulic pump and the motor. If the coupling is skewed, it will inevitably cause vibration and noise.
Second, the noise caused by the hydraulic pump, gas flow and control valve. During the operation of the hydraulic system, noise often occurs under the action of the fluid. Through research, it is found that the factors that cause hydraulic pump noise are related to hydraulic power. When hydraulic power continues to increase, noise will gradually increase. Flow pulsation, pressure shock, etc. will bring certain noise. At the same time, gas flow will also bring noise. If there is air in the oil, bubbles will be suspended in the hydraulic oil and form cavitation in it. When the oil pressure rises to a certain height, the bubbles will be crushed in an instant and bring noise. In addition, there are a large number of control valves in the hydraulic system. These control valves often generate vibration and noise during use due to the influence of back pressure, direction and other factors. |